Titanium is an important structural metal developed in the 1950s, with a small coefficient of thermal expansion and low thermal conductivity. It is a densely packed hexagonal structure at room temperature α At 883 ℃, the phase undergoes an isomeric transformation and becomes body centered cubic β Xiang. Titanium alloy has excellent comprehensive properties such as low density, high specific strength, high temperature resistance, and corrosion resistance, and is one of the most important structural materials for aircraft airframes and engines. With the development of titanium alloy technology, it has also been widely applied in other fields.
1. Introduction to Titanium and Titanium Alloys
Titanium is an important metallic element, and its physical and chemical properties are shown in Figure 1.
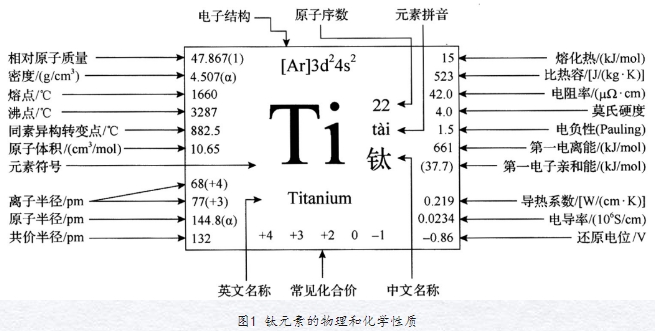
Titanium alloy refers to a new type of alloy formed by adding single or multiple other elements based on titanium element. Titanium has high activity, and most elements can interact with it to form continuous solid solutions, limited solid solutions, metal compounds, covalent compounds, ionic compounds, etc. Alloy elements can optimize their performance by changing their allotropy transition point and phase composition.
Ti can react with most elements in the periodic table. Based on its interaction with titanium, the elements in the periodic table can be divided into four categories: the first category is halogen and oxygen elements, which form ionic compounds with titanium; The second type is transition elements, hydrogen, beryllium, boron group elements, carbon group elements, nitrogen group elements, which form intermetallic compounds and limited solid solutions with titanium; The third type is zirconium, hafnium, vanadium group elements, chromium group elements, and scandium, which form infinite solid solutions with titanium; The fourth category includes inert gas elements, alkali metal elements, alkaline earth metal elements, rare earth elements (excluding scandium), tungsten, and other elements, which do not react with titanium or do not react significantly. There are over 70 elements that can form binary alloys with titanium, divided into αβ Stable αβ- Complete solid solution type β Complete solid solution type β There are four types of eutectoid type. Figure 2 shows the phase diagrams of four types of binary titanium alloys.
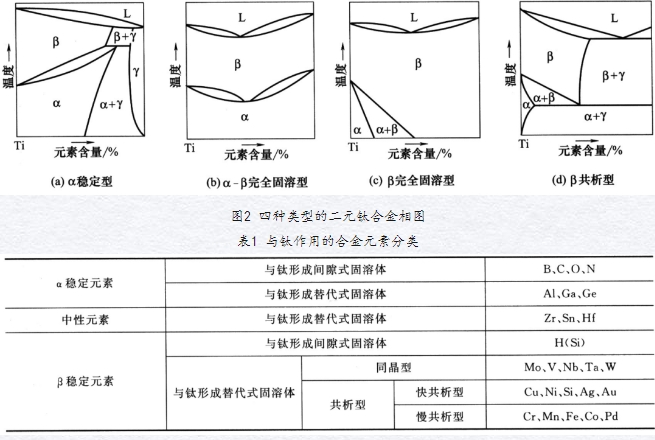
China's titanium industry started as early as 1954. Sponge titanium was prepared by the metal magnesium reduction method in 1955, and titanium slag experiments began in 1956. In 1958, it officially entered the industrial production stage, producing raw materials and profiles such as titanium ingots, titanium tubes, and titanium plates.
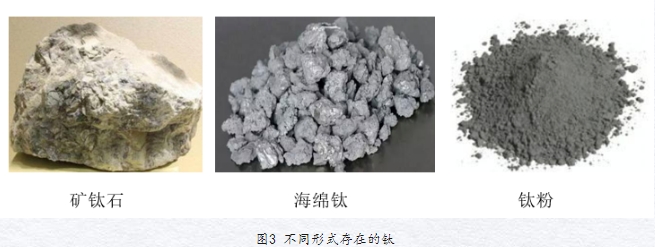
2. Classification of titanium alloys
Titanium has two isomeric structures, namely α Xianghe β When the temperature is lower than the phase transition temperature, titanium has a densely packed hexagonal structure, known as the α ( α- Ti); When the temperature is higher than the phase transition temperature, titanium has a body centered cubic structure, known as β Titanium(( β- Ti). The existence of isomorphism transformation gives titanium alloys distinct characteristics and applications, so they can be classified using various methods.
1) Classify by organizational structure
By utilizing the isomeric characteristics of titanium, different phase stabilizing elements are added to titanium alloys, resulting in differences in phase transition temperature and phase composition content. According to the different matrix structures obtained under room temperature conditions, titanium alloys can be divided into the following three categories: α Titanium alloy β Titanium alloy and a+ β Titanium alloy, its grades are represented by TA, TB, and TC, respectively. Its common classifications are shown in Table 2.
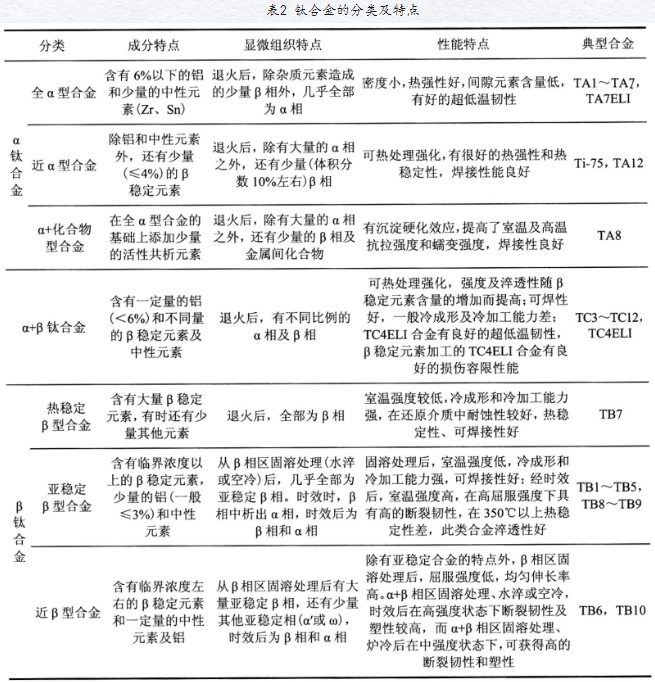
Due to the presence of titanium alloy β The quantity and stability of phases are related to β The types and contents of stable elements are directly related, and can also be determined by β Classification of titanium alloys based on phase stability coefficient. β The phase stability coefficient refers to the values of each β The sum of the ratio of the concentration of stable elements to their critical concentration characterizes titanium alloys β The stability of the phase or β The role of stabilizing elements, Table 3 is commonly used β The critical concentration Ck of stable elements. Calculate the corresponding concentration β The phase stability coefficient Kp, Table 4 shows the Mo equivalent and β Phase stability coefficient.
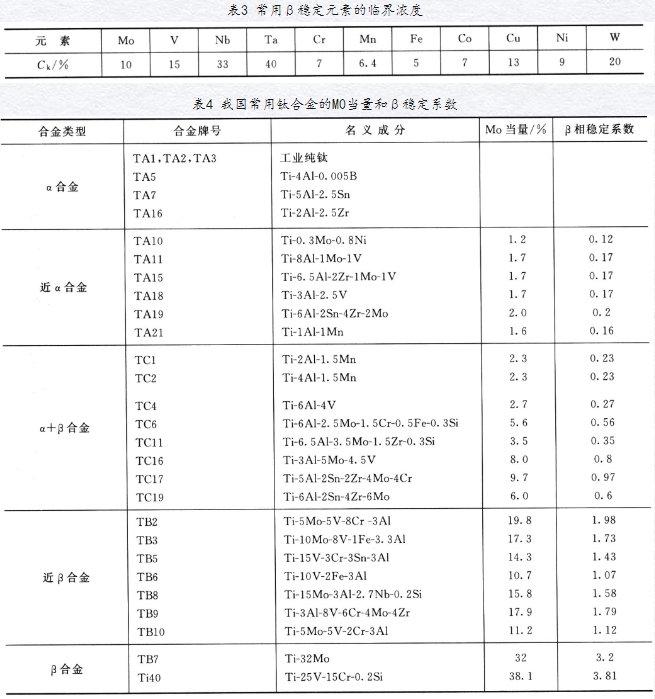
2) Classify according to performance characteristics
As is well known, titanium has ten major characteristics: ① low density, high strength, and high specific strength; ② Good heat resistance; ③ Excellent corrosion resistance; ④ Good low-temperature performance; ⑤ No magnetism; ⑥ Low thermal conductivity; ⑦ Low elastic modulus; ⑧ The tensile strength is close to the yield strength; ⑨ Easy to oxidize at high temperatures Low anti damping performance. In addition, titanium has three special functions: ① shape memory; ② Superconductivity; ③ Hydrogen storage. According to their performance characteristics, titanium alloys can be divided into several categories: structural titanium alloys, heat-resistant titanium alloys, corrosion-resistant titanium alloys, low-temperature titanium alloys, functional titanium alloys, etc.
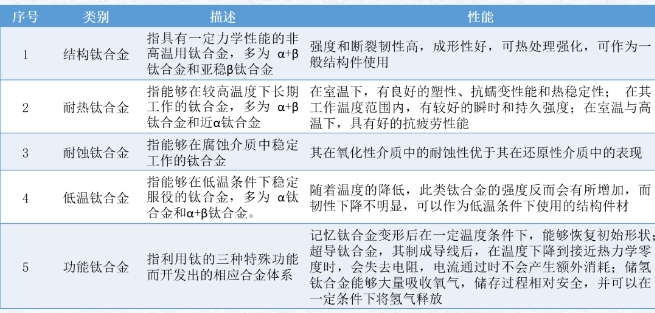
3) Classify by application field
Titanium has many outstanding advantages, known as "space metal", "ocean metal", etc., and has a wide and important use in national defense, military industry, and the national economy. According to its usage in various industries, it can be roughly divided into the following categories:
(1) Aerospace titanium alloys are the main application areas of titanium and titanium alloys, accounting for approximately half of the world's total titanium consumption. According to data, for every 1kg weight loss of an aircraft, its operating costs can be saved by $220-440. For rockets, weight reduction can achieve goals such as reducing launch weight, increasing range, and saving costs. In the aviation industry, titanium is mainly used in the following areas: aircraft engine casings, fan impellers, engine seats, compressor casings, impellers, gas collection pipes, aircraft fuselage structural components, wing structural components, high-pressure oil pipes, tail wing structural components, cabin doors, seat guide wheels, landing gear, etc. In the aerospace field, the main titanium parts used include: rocket engine impellers, fuel tanks, pressure vessels, rocket nozzle sleeves, delivery pumps, satellite connection belts, artificial satellite shells, antennas, manned spacecraft cabins, landing gears, propulsion systems, etc.
(2) Titanium alloys for chemical purposes. Chemical titanium mainly utilizes its corrosion resistance, with pure titanium being the majority. Chemical titanium is the largest sector of titanium consumption in China, accounting for about half of the country's titanium consumption. The main titanium parts used in the chemical industry include oxidation towers, reaction vessels, distillation towers, storage tanks, heat exchangers, pumps, valves, pipelines, electrodes, etc.
(3) Sports and leisure use titanium alloy, which is currently an extremely active field, and various new titanium alloys are continuously used in this field. In China, the use of titanium alloys for sports and leisure accounts for about one-fifth of the total titanium consumption in the country. At present, the main products include golf club heads and clubs, fishing gear, bicycles, snowboards, watches, glasses frames, cameras, titanium drawing boards, etc.
(4) Titanium alloy for power use. Titanium alloys used in power mainly utilize the corrosion resistance of titanium, especially in coastal power stations, which have extremely high requirements for corrosion prevention. In power plants, the main components that use titanium include steam turbine rotor blades, condensate pipes, titanium lined pipes and plates for seawater inlet and outlet in coastal power plants, and steel titanium composite plates for chimney in thermal power plants.
(5) Biomedical titanium alloy. Titanium and titanium alloys have strong corrosion resistance, stable chemical properties, no magnetism, and no toxicity. Their elastic modulus and coefficient of expansion match the human skeleton, making them highly biocompatible. They are gradually replacing stainless steel, Co Cr alloys, and other materials in the biomedical field, opening up another application field for titanium. At present, the main components of biomedical titanium include human bones, teeth, pacemakers, cardiovascular stents, various surgical instruments, etc.
(6) Titanium alloys are used in other fields. In addition to the above-mentioned fields, titanium alloys are also widely used in seawater desalination, shipbuilding, construction, transportation, metallurgy, and other high-tech fields. The corrosion resistance of titanium alloy makes it shine brightly in traditional fields such as shipbuilding and construction; Due to its low density and high specific strength, it is also widely used in transportation and other fields; In terms of high-tech, with the development of titanium alloy performance and improvement of forming technology, it has gradually been applied in high-precision and cutting-edge fields such as large lasers and maglev trains.
4) Classification by grain size
According to grain size, titanium alloys can be further divided into traditional cast coarse-grained titanium alloys (>1000nm) and fine-grained titanium alloys (<1000nm). With the continuous in-depth research on titanium alloys, there is a trend towards the development of titanium alloys towards micro and nano scales. According to grain size, fine-grained titanium alloys can be further divided into three categories: ultrafine grained titanium alloys (100-1000nm), nanocrystalline titanium alloys (1-100nm), and multiscale titanium alloys (with multiple scales coexisting).
3. Different microstructures of titanium alloys
Titanium alloy has α Xianghe β The performance of titanium alloys largely depends on the two basic phases α Xianghe β The properties of the phase itself and its morphology, size, distribution, and proportion in the alloy. β The strength of the phase is higher than α The strength of the phase and the number of slip systems make it easier to withstand plastic deformation. High strength titanium alloys are usually made of β A phase based alloy. α The heat resistance and creep resistance of the phase are both better than β Well, high-temperature titanium alloys are usually α Alloy and Near α Alloy.
The basic structure of titanium alloy is based on α- Ti based α Solid solution and β- Ti based β Solid solution, α Alloy, Near α Alloy and many α+β The matrix of the alloy is α Solid solution, β The matrix of the alloy is β Xiang. The microstructure of titanium alloy mainly depends on the alloy composition, deformation process, and heat treatment process. Typical microstructures include lamellar (Weinstein) structure, basket like structure, equiaxed structure, and bimodal structure, as shown in Figure 4.
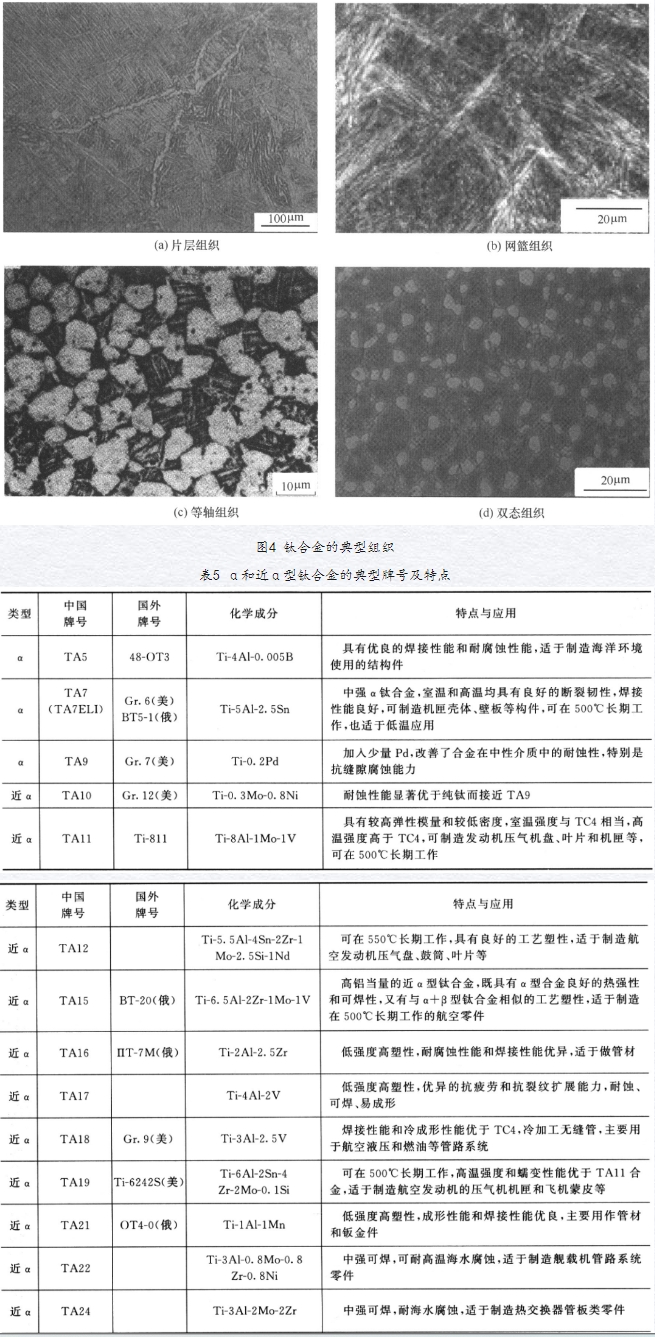
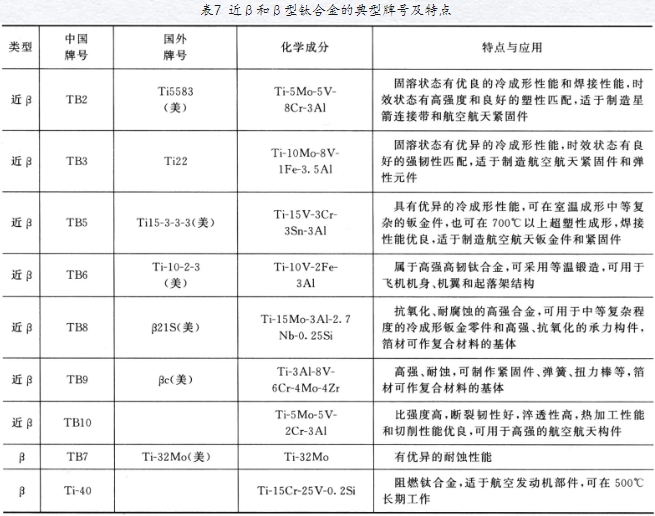
4. Titanium alloys with different properties
1) High temperature titanium alloy
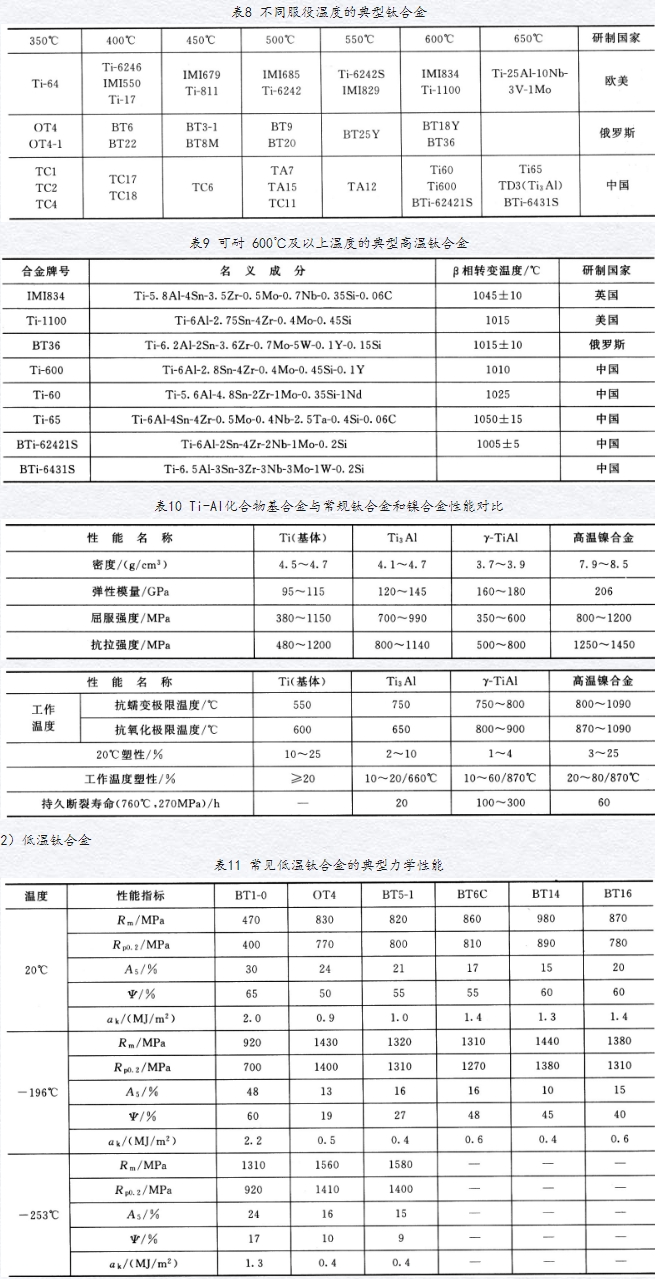
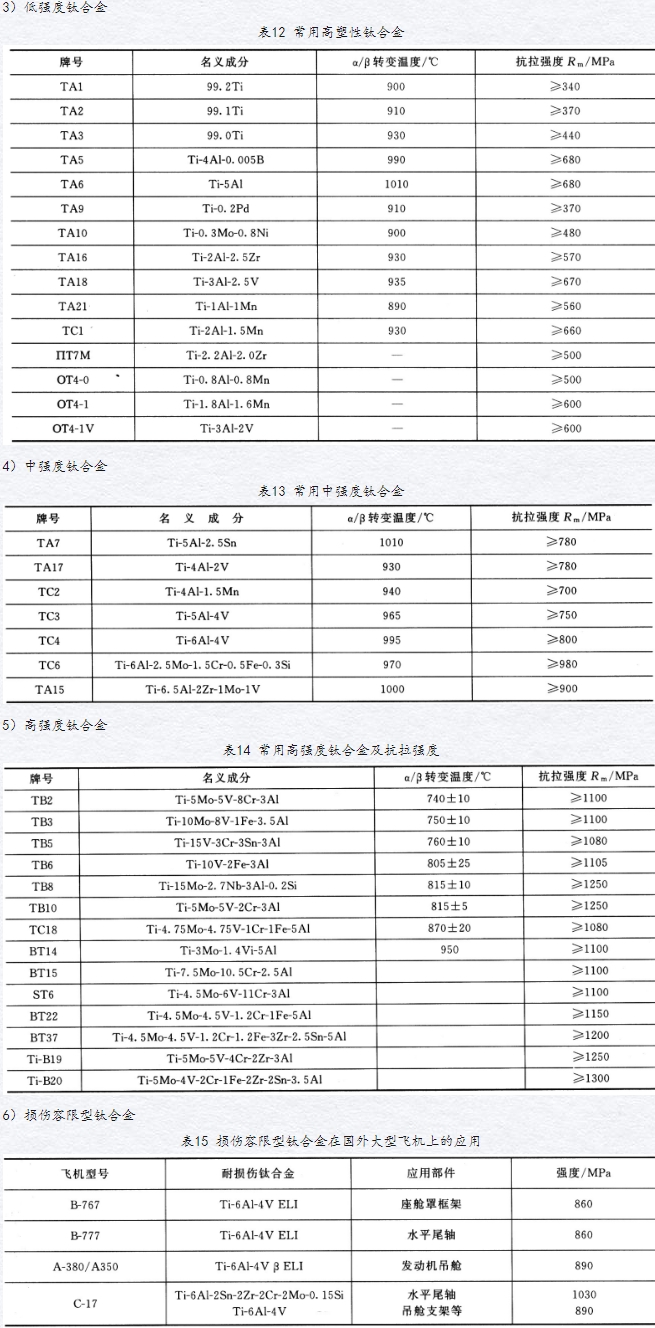
Preparation of titanium and titanium alloys
1. Production process
Figure 5 shows the production process of titanium alloys and materials. Before obtaining titanium materials, the original minerals such as rutile and ilmenite need to be beneficially processed to obtain higher grade concentrate. The concentrate is then processed and purified to obtain high-purity TiO2, which is then oxidized and reduced to obtain TiCl4. The intermediate product, sponge titanium, is produced by crushing and grading the sponge titanium to obtain commercial pure titanium (CP titanium) and products melted from titanium alloys. Titanium alloy materials or products are obtained through pressure processing or powder metallurgy methods.
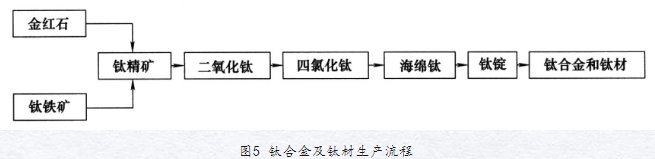
With the continuous development of the titanium industry, the use of powder metallurgy to prepare titanium alloy components has gradually shown its unique advantages. The powder metallurgy method for preparing titanium alloys is a process that uses titanium and titanium alloy powder as raw materials, and then processes the powder into parts through sintering, pressing, and other methods. It is an important component of the near net forming technology for titanium alloys. Titanium alloy powder metallurgy technology has the characteristics of high material utilization, less cutting, and high efficiency, which can to some extent avoid defects such as component segregation and uneven structure generated by casting.
At present, the common production methods for titanium powder in the world include hydrogenation dehydrogenation method, conductive body intervention reaction method, Armstrong process, preform reduction method, high-energy ball milling method, metal hydride reduction method, continuous molten salt flow method, plasma hydrogen reduction method, gas-phase reduction method, atomization method, etc. Among them, the hydrogenation dehydrogenation method has the characteristics of simple operation and low cost, and is the most commonly used method for titanium powder production. The hydrogenation dehydrogenation method is a process that produces brittle hydrogenated titanium from sponge titanium after hydrogen absorption, which is mechanically crushed and dehydrogenated under vacuum and high temperature conditions to produce pure titanium powder. The process flow of hydrogenation and dehydrogenation is shown in Figure 6. The currently widely used industrial titanium production method is the magnesium reduction method. Figure 7 shows the process of producing sponge titanium using magnesium reduction method, using refined titanium tetrachloride as the raw material and metallic magnesium under argon protection as the reducing agent.
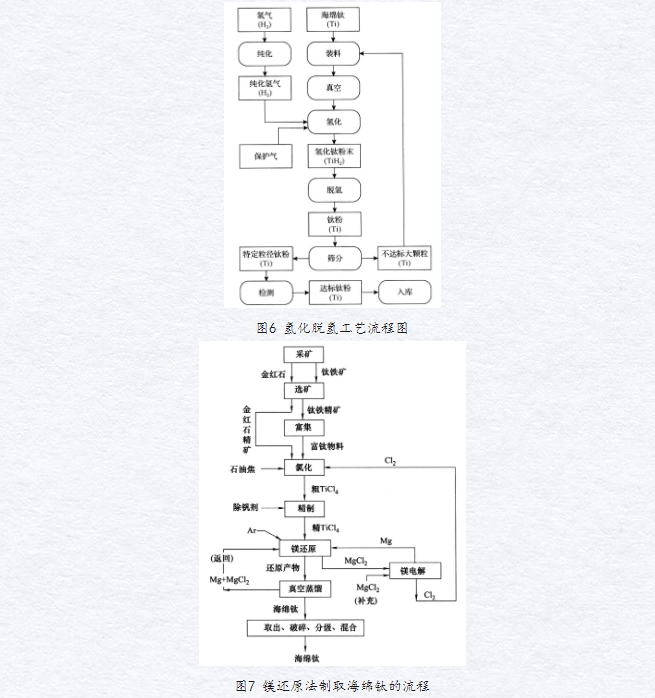
Figure 8 shows the production process of different types of titanium materials. Sponge titanium is melted and cast to obtain dense titanium ingots, which are then processed under different pressures to obtain different types of titanium materials. The ring parts are produced by ring rolling, the plates are hot-rolled and cold-rolled, the seamless pipes are produced by extrusion rolling method, and the welded pipes are produced by bending forming welding method. Due to the high deformation resistance and narrow processing temperature range, the production difficulty and high technical content of titanium alloy materials have hindered the development of the titanium industry.
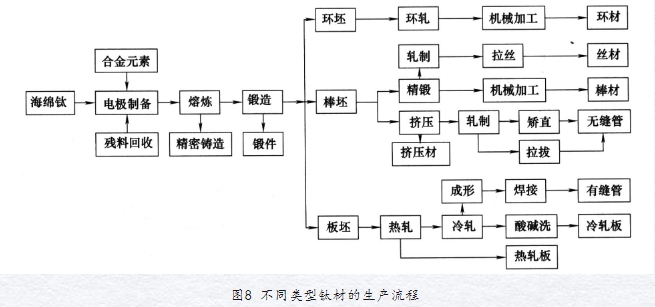
At present, the methods for preparing titanium alloy powder include plasma rotating electrode method, electron beam rotating disc method, vacuum atomization method, atomization method, rapid condensation method, mechanical alloying method, etc. The mechanical alloying method can quickly obtain activated titanium alloy powder, as shown in Figure 9. In the process of preparing titanium alloy powder by mechanical alloying, titanium powder and other metal powders are first mixed in a ball mill according to the required ratio. Then, through the rotation or vibration of the ball mill, the metal powder is continuously collided and squeezed, causing repeated deformation, fracture, cold welding, and diffusion, ultimately achieving the goal of powder alloying.
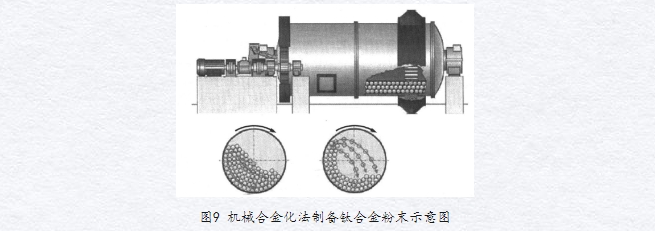
2. Melting casting
The raw materials used for melting titanium and titanium alloys include sponge titanium, titanium and titanium alloy return furnace materials, pure metals, and intermediate alloys. Titanium has a very high chemical activity and a high melting point. At the melting temperature, titanium is prone to chemical reactions with gases and other elements, refractory materials (various oxides), and refractory materials used in mold making. Therefore, titanium alloy melting and casting must be carried out under vacuum or inert gas protection, leading to an increase in production costs.
1) Ingot casting and production process flow
The commonly used titanium alloy melting methods include vacuum consumable arc melting (VAR), cold furnace bed melting (CHM), vacuum non consumable arc melting (NC), electroslag melting (ESR), and vacuum induction melting (CCM). The vacuum consumable arc melting method has become the main melting method for titanium alloys due to its economic efficiency, and the cold bed furnace melting has become the preferred melting method for titanium alloys used in aircraft engines due to its high quality. Figure 10a shows the process flow of vacuum consumable arc melting. The raw materials are first prepared into electrode blocks (with a density greater than 3.2g/cm3), and then welded into electrodes of the required cross-section and length, which are melted in a vacuum consumable arc furnace. The produced ingots have good crystalline structure and relatively uniform composition, with less volatile loss. However, due to the limited degassing and impurity removal ability of vacuum consumable arc melting, the finished ingots need to go through at least two melting processes.
An electric furnace that uses an electric arc to directly heat and melt metal in a vacuum furnace is called a vacuum arc furnace. It mainly relies on the steam of the molten metal to generate an arc. The shape of the ingot end face is limited to a circular shape, and it is divided into a consumable furnace and a non consumable furnace according to whether the electrodes are consumed (melted) during melting. Figure 10b is a schematic diagram of the structure of a vacuum consumable arc furnace.
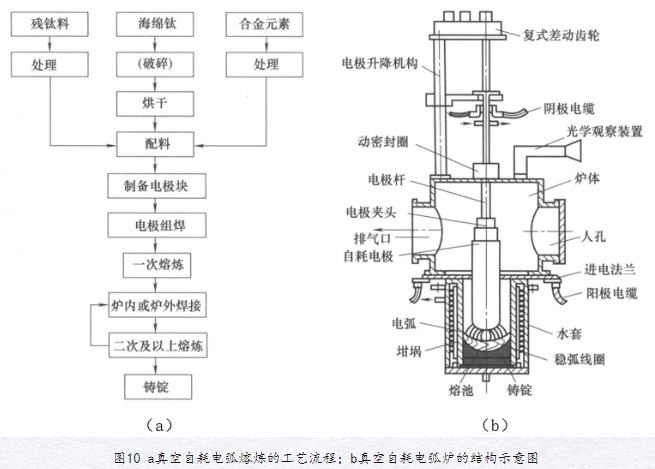
Figure 11a shows the process flow of cold bed furnace melting. The furnace material to be melted enters the cold bed and is subsequently melted, refined, and solidified. The ingots can be round, flat, or hollow. The cold bed furnace melting equipment consists of a heat source, a cold bed, and a crystallizer. There are two types of heat sources: electron beam and plasma, which are respectively called electron beam cold bed furnace melting (EBCHM) and plasma beam cold bed melting. They are melted and solidified under vacuum or argon protection. Figure 11b is a schematic diagram of the structure of an electron beam cooling bed furnace, mainly composed of a melting chamber, vacuum system, electron gun, electron beam control system, feeding system, crucible and ingot pulling mechanism, power supply system, water cooling system, observation device, etc.
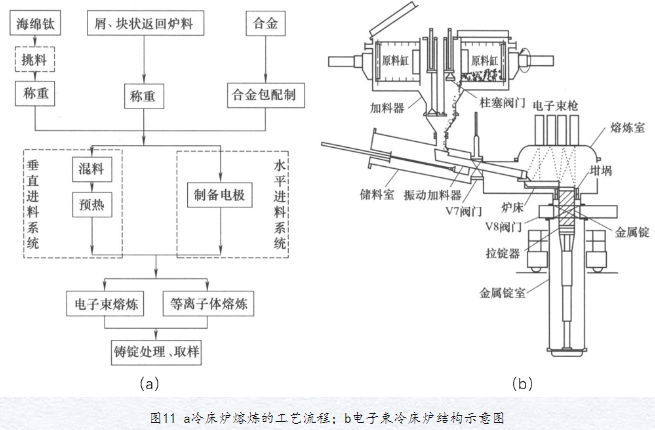
Except for different heat sources, the structure of plasma cooling bed furnace is basically the same as that of electron beam cooling bed furnace, as shown in Figure 12, including heat source system, cooling bed, crystallizer, feeding mechanism, vacuum system, water cooling system, control system, inflation system, etc.
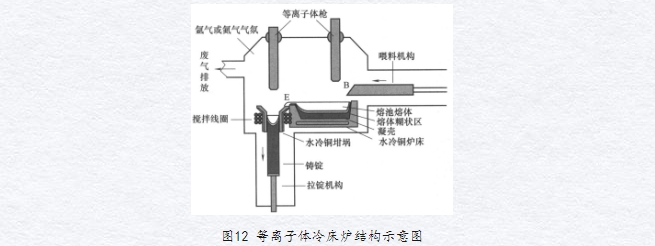
Vacuum Non Consumable Arc Melting (NC) is a non consumable melting process conducted in a vacuum arc furnace. It uses water-cooled copper electrodes to melt the titanium in the crucible using the heat of the arc, and then pours it into a water-cooled copper mold to form an ingot, or continuously adds materials to melt and solidify it into an ingot in the water-cooled copper crucible. In order to prevent arc damage to the electrodes, water-cooled copper electrodes can self rotate or have a rotating magnetic field. The NC method can directly use loose materials, avoiding the trouble of preparing electrodes, and is suitable for the recovery and smelting of residual titanium materials.
The electric slag melting method (ESR) uses the heat generated by electric current passing through the electric slag to melt and refine metals. It can be used as furnace material with consumable electrodes, water-cooled non consumable electrodes, and bulk furnace materials. CaF2 is added to provide insulation between the melt and the crucible. When using ESR to melt titanium, a vacuum argon filled atmosphere must be used for remelting in a water-cooled copper crucible and under the protection of electric slag, commonly known as electric slag remelting. The ESR method can directly melt ingots of different shapes, with good surface quality, no need for milling or car skin, and low equipment investment cost. However, the dehydrogenation effect is poor and the purification ability is low.
Vacuum induction melting (CCM), also known as cold crucible melting, is a slag free water-cooled segmented copper crucible induction melting method. Four curved copper blocks are combined to form a copper crucible, with ceramic insulation between the blocks. The copper crucible and the induction coil are immersed in a water jacket, and thermal energy is generated through electromagnetic induction to melt titanium. The use of high-purity copper can improve electrical efficiency (reduce impedance), keep the crucible water-cooled and not in contact with the melt, and can coexist with high melting points or active element melts without reaction. Splitting is to avoid the shielding effect of conductive crucibles on the electromagnetic field. The gap between two copper blocks forms an enhanced magnetic field, and the strong stirring generated by the magnetic field makes the chemical composition and temperature consistent. Without the need to make electrodes, high-quality ingots with uniform composition and no crucible pollution can be obtained in one go. CCM can be used in vacuum or any atmosphere, especially suitable for melting active metals, high-purity metals, refractory metals, radioactive materials, etc. For special materials, CCM is a particularly promising melting technology.
1) Casting of castings
Most deformed titanium alloys can be used for casting, among them. Single phase or α Based on phase and containing a small amount β Phase titanium alloy (in annealed state β The number of phases generally does not exceed 10%, which is more suitable for casting. However, the molten state of titanium will almost react with all refractory materials and gases, greatly increasing the difficulty of casting. Melting and pouring must be carried out under inert gas protection or vacuum, and crucibles made of ordinary refractory materials cannot be used. The melting of titanium alloy castings is usually carried out using a vacuum consumable electrode arc solidification furnace. Under the action of the arc, the titanium alloy is melted, forming a solidification layer in a forced cooling copper crucible. The titanium liquid does not directly contact the water-cooled copper crucible, which can avoid contamination from the crucible. Figure 13 shows a 150kg vacuum consumable electrode arc shell furnace, which has advantages such as simple structure, low maintenance cost, and easy scalability. However, it has disadvantages such as requirements for the shape of raw materials, difficulty in recycling waste, and constraints on melting rate.
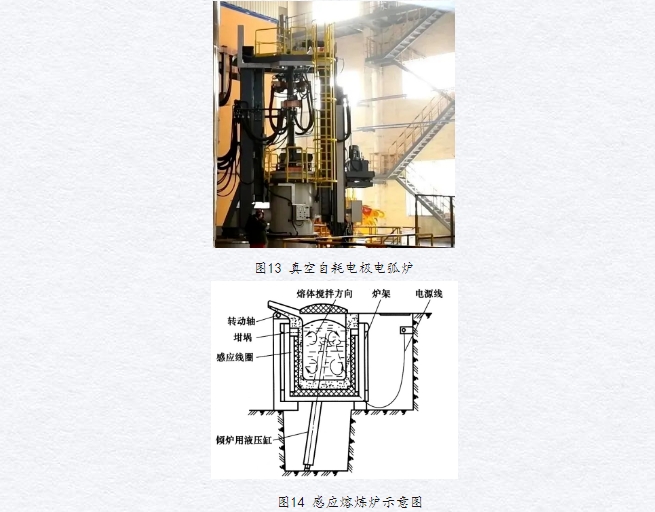
Figure 14 is a schematic diagram of an induction melting furnace, which uses alternating magnetic field force to melt and suspend the metal without contact with the crucible. It can directly use waste and sponge titanium as melting materials, with strong stirring ability, easy alloying, uniform composition and temperature, but high equipment cost and low production efficiency. The main difficulty in titanium alloy casting is the easy generation of gas. It is usually necessary to set up a reasonable exhaust duct in the pouring system to ensure good permeability of the mold. Gas content can be reduced through methods such as vacuum degassing, centrifugal casting, or pressure casting.
3. Titanium forming
The traditional titanium forming methods mainly include forging, rolling, extrusion, drawing, stamping, spinning, etc., which can process plates, strips, strips, foils, tubes, bars, shapes, wires, as well as forgings, stamped parts, spinning parts and other products. However, pressure processing of titanium and titanium alloys has disadvantages such as high deformation resistance, poor room temperature plasticity, high yield ratio, large rebound, sensitivity to cracks and notches, narrow plastic forming range, easy adhesion of molds during deformation, and easy adsorption of harmful gases during heating. Therefore, pressure processing of titanium is more difficult than that of steel, aluminum, and copper, resulting in high production costs of titanium alloys and hindering their widespread use.
1) Pressure processing
At low temperatures, α Titanium alloy has a dense hexagonal crystal structure with fewer slip planes, making plastic deformation relatively difficult; As the deformation temperature increases, the number of slip planes increases, gradually leading to some densely packed hexagonal lattices. Transforming into a body centered cubic lattice β Phase, plasticity correspondingly increases; When the deformation temperature exceeds the phase transition point, it enters β When in the phase zone, the plasticity of the alloy is greatly improved, while the deformation resistance is greatly reduced. Therefore, titanium and titanium alloys are usually subjected to hot deformation.
Forging includes forging and stamping. Stamping can process parts with thin walls and complex shapes, resulting in high-strength, high rigidity, and lightweight parts. The processed parts have stable quality, good consistency, good interchangeability, high material utilization, and high productivity. The forging of titanium alloys can be divided into α+β Forging β Forging, near β Forging and Precision β Forging, Figure 15 shows a schematic diagram of different forging processes and temperatures for titanium alloys. Different forging processes can result in different forging structures.
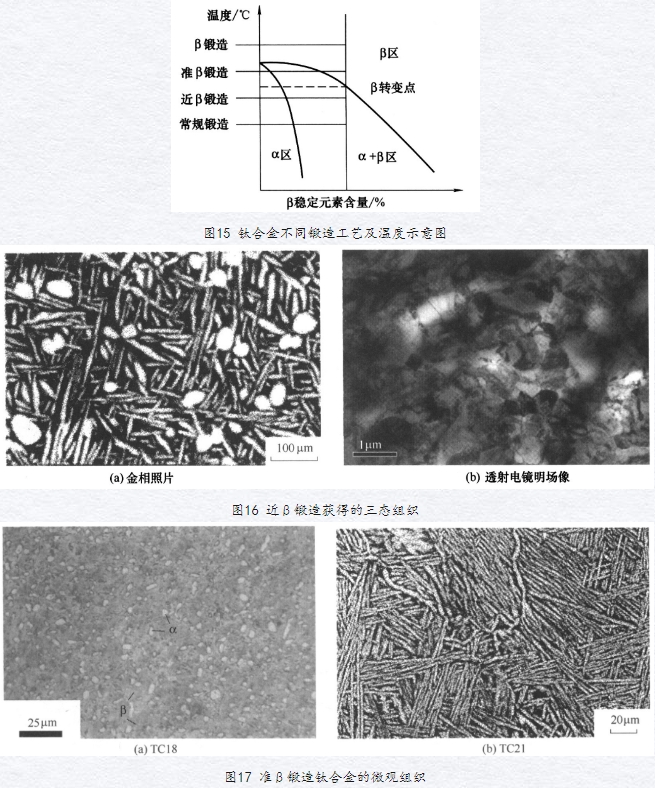
Due to the lower thermal conductivity of titanium alloys compared to metals such as copper, aluminum, iron, and nickel, the cross-sectional temperature of large billets is not easily uniform during heating. After the billets are discharged from the furnace, the surface cools quickly, resulting in large internal and external temperature differences, which can easily lead to cracking and uneven deformation. In order to reduce the cooling rate on the surface of the billet, it is important to fully preheat the mold and the tools in contact with the billet. Figure 18 shows the temperature state of the mold and forgings using different forging methods. Hot die forging and isothermal forging can produce large and extra large forgings, and can produce near net shaped forgings, achieving the optimization of forging structure and properties.
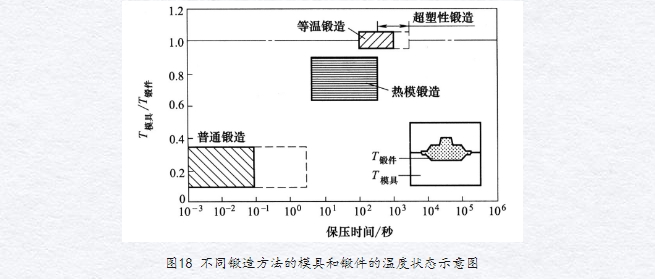
(2) Squeeze
The extrusion method is suitable for the production of small batch, multi variety, and multi specification titanium alloy pipes, bars, profiles, and wire billets, especially for thin-walled pipes and profiles with complex cross-sections, as well as ultra thick walled pipes. Titanium and titanium alloys often use hot extrusion, α Type titanium alloy α+β Type alloys are typically used in(( α+β)/β Squeezing at temperatures below the phase transition point, β Type titanium alloys usually require a higher extrusion temperature and are required to be in the β The temperature range of the phase, however, when the temperature is too high, β The rapid growth of phase grains leads to a decrease in plasticity. For titanium alloys that are difficult to deform and have high brittleness, such as flame retardant titanium alloys and TiAI based intermetallic compounds, sleeve extrusion is the most practical and feasible pressure processing method.
(3) Rolling
Rolling can be used to produce titanium and titanium alloy plates, strips, foils, rods, tubes, and profiles, especially thin-walled and variable cross-section profiles. The produced titanium materials have good surface quality and stable internal quality. The rolling of titanium includes hot rolling, warm rolling, and cold rolling. Warm rolling can be used for 2-5mm thick plates, and cold rolling can be used for thinner sizes. The cold rolling deformation between two annealing cycles is generally 15% -60%.
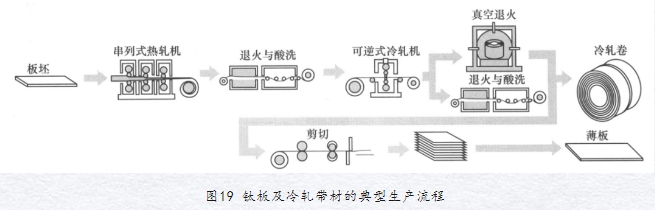
Bars and simple cross-sectional profiles can be rolled using horizontal pass rolling, and the optimal pass series can be designed according to the product shape. Compared to steel rolling, titanium pass rolling has a larger coefficient of expansion.
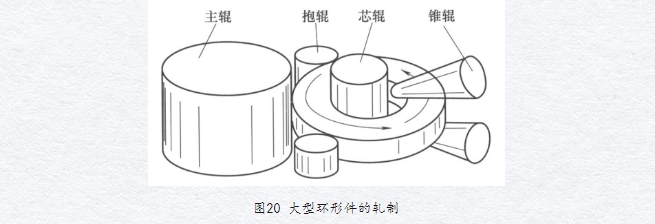
(4) Pulling
Drawing can produce titanium alloy pipes, small diameter bars, and wires. In order to prevent mold sticking, the billet needs to be treated with phosphate or oxidation, coated with graphite, molybdenum disulfide, or lime based lubricants. For titanium alloys that are difficult to cold draw, warm drawing can be used.
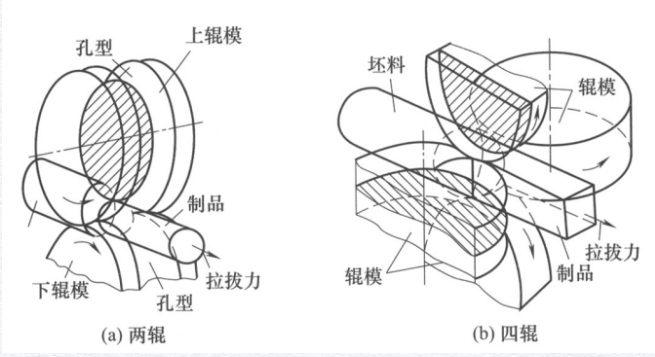
Figure 22 is a schematic diagram of die less drawing, which uses an induction coil or laser to locally heat and soften the titanium material, and applies tension to make it finer. The advantage is that it does not require drawing dies and lubricants, and has a high deformation rate and efficiency.
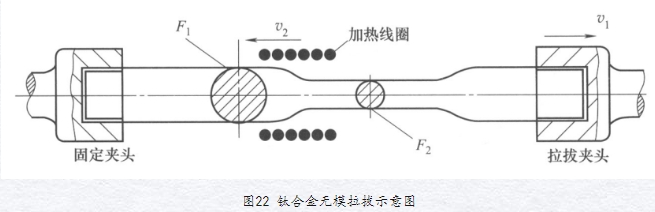
(5) Spinning
Spinning is divided into ordinary spinning and strong spinning, mainly used for forming thin titanium sheet parts and hollow rotary body parts. It has obvious advantages in forming large-diameter and thin-walled parts. The rotating metal blank produces continuous local plastic deformation and forms into rotary body parts. Its strength and hardness are increased by 15% -25% compared to the blank, and its dimensional accuracy is second only to mechanical processing. Figure 23 shows a photo of the spinning machine and a schematic diagram of the spinning process.
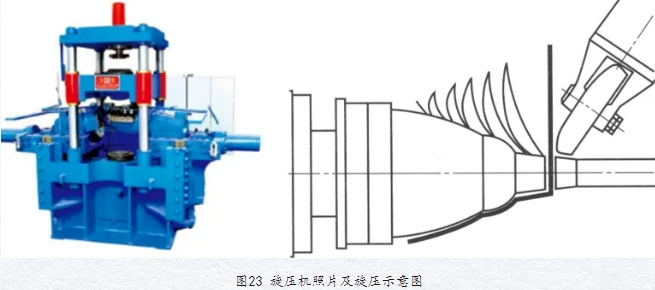
The deformation characteristics of ordinary spinning are that the metal slab mainly produces diameter shrinkage or expansion, while the thickness of the blank remains basically unchanged. It can be divided into deep drawing spinning, reduced diameter spinning, and expanded diameter spinning, as shown in Figure 24.
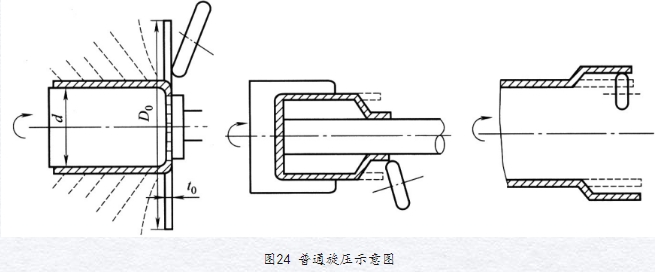
2) Near net forming
Near net forming technology can achieve near net dimensional forming of titanium alloy components with complex shapes, which can be used as components with only a small amount of processing or no processing, reducing the input cost and processing steps of raw materials, and products have similar structures and properties to traditional processes.
(1) Precision casting
The precision casting of titanium alloy integral structural components mainly includes investment casting and lost foam casting, which can directly cast titanium alloy parts with complex and thin-walled shapes, saving a lot of mechanical processing procedures, and the material utilization rate can reach 75% -90%. Investment casting includes graphite investment casting, tungsten surface layer investment casting, and oxide ceramic investment casting. It can cast complex shaped castings, with flexible production and strong adaptability. It is suitable for blank impellers and hollow blades, as well as precision castings that are resistant to high temperature, wear, and corrosion. For titanium alloy components such as blades, impellers, and nozzles that require precise shape and size, mass production using investment casting can not only ensure the accuracy and consistency of casting shape and size, but also avoid stress concentration caused by residual tool lines after mechanical processing. Expendable pattern (EPS foam) casting can produce large structural parts, which solves the problems of long production cycle, high cost of investment casting mold and wax mold sensitive to temperature and easy to deform. The disappearing mold model usually adopts machining and foaming forming. For single or small batch structural parts, especially curved structure castings such as impellers, it has the characteristics of low cost, high casting accuracy, and good dimensional consistency, which can fully meet the growing requirements of large-scale, precision, and integral casting.
(2) Powder metallurgy
Powder metallurgy (PM) is the process of using metal powder (or a mixture of metal powder and non-metal powder) as raw material, mixing or solid-state alloying, pressing and forming, and sintering at a temperature below the melting point of the metal, using atomic diffusion between powders to combine them. Complex workpieces that cannot be formed using traditional casting and pressure processing methods can be achieved through powder metallurgy for near net forming, with little or no cutting, and a raw material utilization rate of over 95%. The material composition and density of powder metallurgy are controllable, and high alloying titanium alloys and various types of products such as porous, semi dense, or fully dense can be prepared. The microstructure of the products is uniform, without component segregation, and the properties of the prepared titanium alloy components can be comparable to those of casting and forging. In the titanium industry, various forming technologies have been developed, including molding, powder forging, powder hot pressing, powder extrusion, powder rolling, isostatic pressing, injection (spray) forming, explosive forming, and combustion synthesis (self propagating high-temperature synthesis). Figure 25 is a schematic diagram of the injection molding machine and powder injection molding process
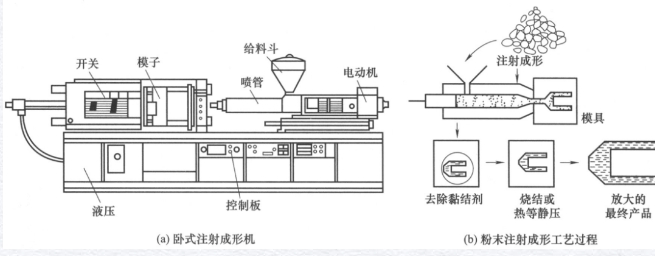
Densification is the key to improving the quality of powder metallurgy products. For titanium alloy powder metallurgy structural parts used in aviation, full densification is necessary. However, full densification is very difficult for high melting point and high activity titanium alloys. In order to improve the tensile and fatigue strength of powder metallurgy titanium alloys, subsequent processing or heat treatment or chemical heat treatment after densification is generally adopted. The commonly used subsequent hot working methods include hot pressing, hot isostatic pressing, hot extrusion, and hot forging. Figure 26 is a schematic diagram of the hot isostatic pressing process.
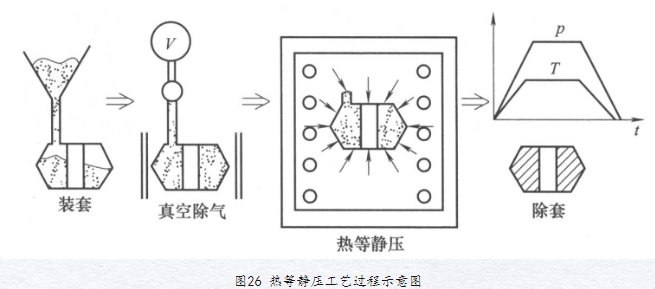
(3) Superplastic forming
Having small equiaxed crystals or α+β Dual phase titanium alloys have significantly reduced deformation resistance, improved flowability and filling ability at higher deformation temperatures and lower strain rates, and possess soft properties that can be blown and extruded. By using superplastic forming (SPF) technology, difficult to deform alloys can be formed into complex components with only a small amount of stress, eliminating the need for mechanical processing, riveting, and other processes. Superplastic isothermal forging is the process of heating a mold to the superplastic forming temperature of a metal, forging it at a low strain rate, and undergoing long-term creep to achieve the formation of thin-walled, high rib, complex or difficult to deform titanium alloy forgings. It has shown significant advantages and application prospects in the field of aerospace manufacturing, especially in the production of compressor blades for engines and large aviation complex forgings. Superplastic sheet metal forming includes methods such as vacuum forming, pneumatic forming, and die pressing, among which pneumatic forming is the most widely used method for sheet metal superplastic forming in the aerospace field. Figure 27 is a schematic diagram of superplastic forming of titanium sheet material, usually protected by argon gas.
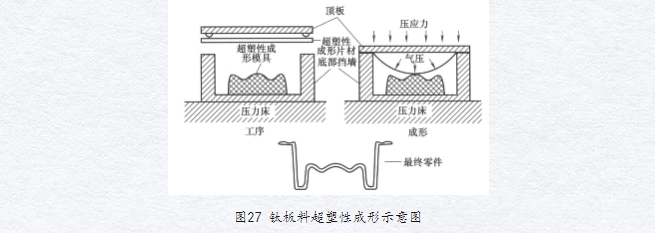
(4) Explosive forming
Explosive forming is the use of explosives, gunpowder, combustible gases, and other energy sources to release enormous chemical energy at the moment of explosion, generating high-pressure shock waves on metal billets, causing them to undergo plastic deformation and adhere to the mold at a certain speed. Explosive forming mainly includes explosive deep drawing and explosive bulging, as shown in Figure 28
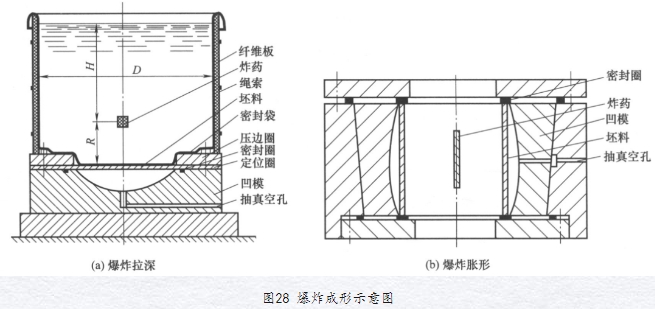
(5) Additive manufacturing
Additive manufacturing is a manufacturing method in which materials are gradually accumulated. By stacking them point by point, it is possible to produce parts of any complex shape, and different materials can be generated in different parts of the workpiece. This is something that traditional technologies such as casting and forging cannot achieve. Compared to traditional subtractive or equal material manufacturing methods, additive manufacturing eliminates the constraints of molds, specialized tools, and calipers, and can achieve "free manufacturing". The manufacturing process is independent of the geometric shape of the manufacturing prototype, and the reproducibility and interchangeability of the prototype are high, greatly reducing processes and shortening processing cycles. The more complex the product structure, the more significant the advantages of additive manufacturing.
3) Composite forming
(1) Titanium metal composite forming
Explosive bonding, rolling bonding, and extrusion bonding are effective methods for processing titanium composite materials. Composite materials and components such as titanium steel composite plates, titanium copper composite rods, and titanium dissimilar metal transition joints have been produced. Titanium steel composite plates have both the high strength of steel and the excellent corrosion resistance of titanium. Multiple thicknesses and widths of composite plates can be produced using direct rolling method, casting rolling method, explosive rolling method, and explosive method. Titanium alloy belongs to the metal that is not easy to roll composite at room temperature. Hot rolled composite also has problems such as complex billet pre-treatment, easy reaction between metals to form brittle compounds, and low yield. Explosive composite and conventional rolling can be used to produce composite plates, strips, pipes, or bars of titanium and different metals. Figure 29 shows the schematic diagram of explosive bonding and the titanium steel plate formed by bonding.
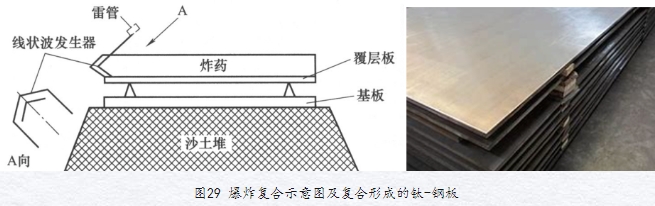
(2) Superplastic forming and diffusion bonding
When the superplastic temperature of the material is similar to the diffusion bonding temperature, a single heating process can be used to complete the two processes of superplastic forming and diffusion bonding, and to manufacture locally reinforced or integrally reinforced components, replacing screw and riveting. Figure 30 is a schematic diagram of using superplastic forming/diffusion bonding (SPF/DB) to produce lattice shaped structural components.
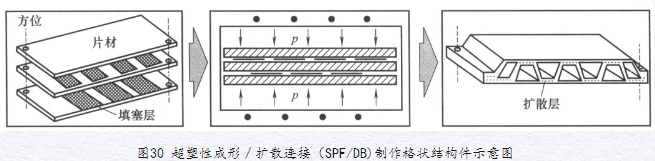
Figure 31 shows the basic structural form and forming schematic diagram of SPF/DB parts. Three layer and four layer plate structural components made of titanium alloy are widely used in the aerospace field. Compared with traditional riveting or bonding, their overall integrity and connection strength are much higher.
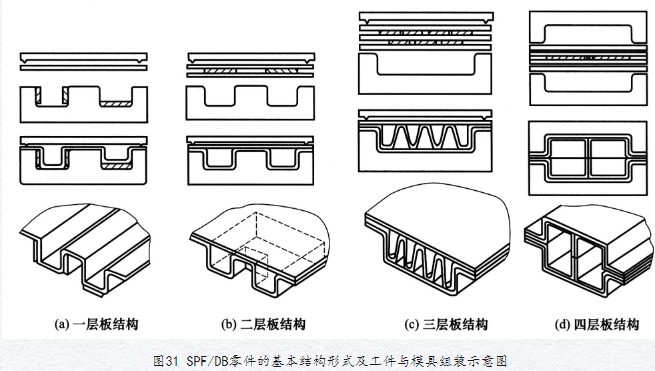
4. Titanium material heat treatment
The heat treatment of titanium materials includes annealing, solid solution, and aging, with the main purpose of eliminating internal stress and work hardening, causing the microstructure to undergo recovery and recrystallization, stabilizing the microstructure and properties, and strengthening.
1) Solid state phase transformation of titanium alloys
The solid-state phase transformation of titanium alloys has diversity and complexity, and many phase transformations may occur in titanium alloys, including allotropy transformation, eutectoid transformation, martensitic transformation, and ω Phase transition.
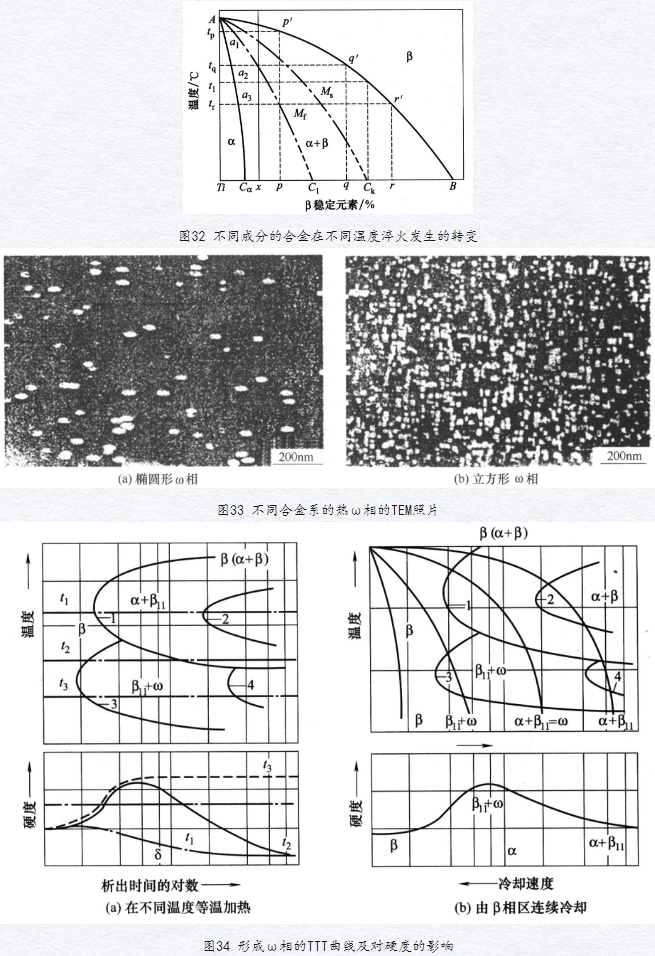
2) Titanium annealing
Annealing is a heat treatment process based on microstructural changes such as recovery and recrystallization, with the main purpose of relieving stress, improving plasticity, and stabilizing microstructure. It includes ordinary annealing, stress relief annealing, complete annealing (recrystallization annealing), isothermal annealing, double annealing, vacuum annealing, etc. Isothermal annealing and double annealing are mainly used for α+β Type titanium alloy.
(1) Annealing method
Ordinary annealing is usually applied before metallurgical products leave the factory, with the aim of relieving the basic stress of titanium alloy semi-finished products, and having high strength and plasticity that meets technical requirements, as shown in Figure 35. The annealing temperature is generally equivalent to or slightly lower than the starting temperature of recrystallization.
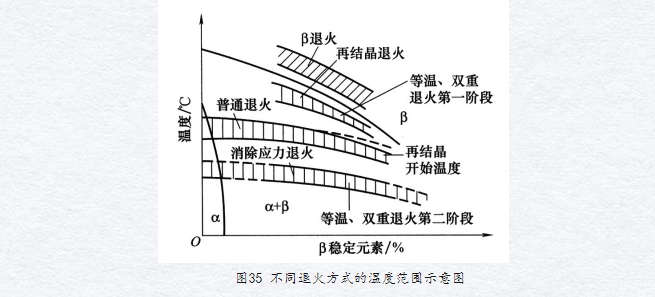
Stress relief annealing, also known as incomplete annealing, aims to eliminate internal stresses generated by casting, cold deformation, and welding, and restore the microstructure from a metastable state to a stable state.
Complete annealing can obtain recrystallized structure and complete softening, also known as recrystallization annealing. The annealing temperature is best between the recrystallization temperature and the phase transition temperature, usually 100-200 ℃ above the starting temperature of recrystallization. Excessive temperature leads to oxidation and grain growth, while low temperature leads to incomplete recrystallization. Air cooling is used as the cooling method.
Isothermal annealing is the process of heating titanium alloys above the recrystallization temperature but below(( α+β)/β Keep the phase transition point within the temperature range of 30-100 ℃ for a period of time, and then transfer it to the β The furnace is insulated within a highly stable temperature range (usually below the recrystallization temperature), and finally air-cooled to room temperature. Isothermal annealing is mainly used for containing β High stability elements. α+β Dual phase titanium alloy, suitable for thermal strength titanium alloys such as TC6 and TCll.
Double annealing includes two heating and insulation cycles and two air cooling cycles. The first cycle is high-temperature annealing, and the second cycle is low-temperature annealing. High temperature service titanium alloys usually require double annealing, or even triple annealing, to ensure their structural and performance stability under high temperature and long-term stress.
(2) Organizational changes during slow cooling process
Heated titanium alloy self β When the phase zone cools slowly, it can be obtained α、α+β or β Organization.
3) Solid solution quenching
The solid solution treatment process should ensure that the alloy elements are fully dissolved in the solid solution. However, due to the fact that the alloy elements β The diffusion coefficient in the phase zone is relatively high, and heating titanium alloy to the high-temperature phase zone is prone to the formation of coarseness β Grain structure, therefore, the first step in solution treatment is to determine the appropriate solution temperature. The solid solution time is affected by the alloy composition, solid solution temperature, and cross-sectional size of the workpiece. For two-phase alloys, the insulation time should be longer. Lowering the solid solution temperature should correspondingly extend the insulation time. The larger the cross-sectional size of the workpiece, the longer the insulation time.
4) Artificial aging
Obtained from titanium alloy quenching α' ( α'') Xiang ω Phase and subcooling β Phase (metastable) β Phase is thermodynamically unstable, and decomposition occurs when heated to a certain temperature. Before transitioning to an equilibrium phase, it undergoes a series of complex transition stages, and the final structure corresponds to the equilibrium structure on the phase diagram. For isomorphic forms β Alloy, decomposition products are α+β, For eutectoid type β Alloy, decomposition products are α+ TixMy.
(1) Supercooling β Phase decomposition
Densely packed hexagonal structure α Phase in body centered cubic structure β Nucleation in the phase matrix is relatively difficult and metastable β The decomposition of the needs to go through some intermediate decomposition processes to generate transition phases and then transform into equilibrium α The type of transition phase generated depends on the heating temperature and alloy composition. Figure 36 shows the isothermal transformation curves of Ti Cr alloys with different compositions, with higher Cr content leading to undercooling β The more stable it is, the longer it takes for the decomposition to start and end, and the more the C curve shifts to the right
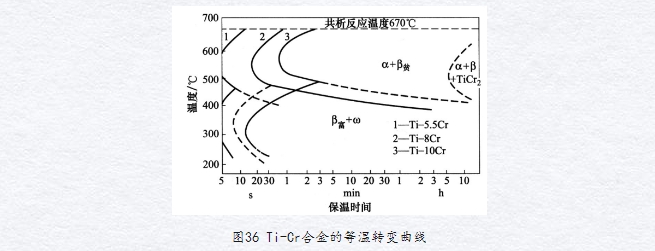
(2) Decomposition of martensite
The decomposition of martensite depends on factors such as the composition of martensite, the properties of alloying elements, the phases coexisting with martensite in the quenched structure, and the heat treatment system β The concentration of stable elements also varies with the quenching temperature, and the changes in these factors can cause changes in the stability of martensite, leading to different decomposition processes.
(3) Determination of artificial aging process
When heated to a certain temperature for artificial aging, the metastable phase obtained through quenching decomposes in a certain way, resulting in a strengthening effect. The strengthening effect depends on the type, quantity, composition of the metastable phase, and the dispersion of the precipitated phase, which decomposes into dispersed phases α Xiangor β Phase can significantly strengthen the alloy. For titanium alloys with a certain composition, the aging process of the alloy can be determined based on the TTT diagram (isothermal transformation kinetics curve) of the temperature time transformation relationship during the aging process. Figure 37a shows the TTT diagram of Ti-11.5Mo-6Zr-4.5Sn alloy, and Figure 37b shows the TTT diagram of Ti-4.5Cr alloy. The Y phase is TiCr2, and the shape and position of the C curve vary with different alloy compositions, resulting in changes in the corresponding aging process.
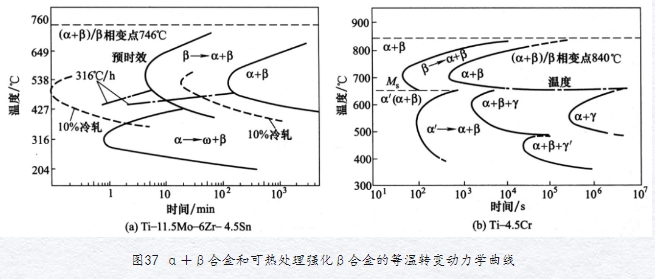
The application of titanium alloys
1. Titanium alloy for aircraft
Titanium alloy not only has high specific strength, but also has advantages such as wide temperature range, good corrosion resistance, and electrochemical compatibility with polymer based composite materials, which can effectively reduce the weight of aircraft. Titanium is an indispensable raw material in aircraft fuselage and engine components, and the amount of titanium used in aircraft accounts for about half of the global production of metallic titanium.
Figure 38 shows a schematic diagram of the application of titanium in aircraft. Titanium is mainly used in the framework of the fuselage, central wing box, wing beams and ribs, fuselage and wing skin, tail cover and vertical tail components, landing gear components and wheels, engine compartment and engine, etc.
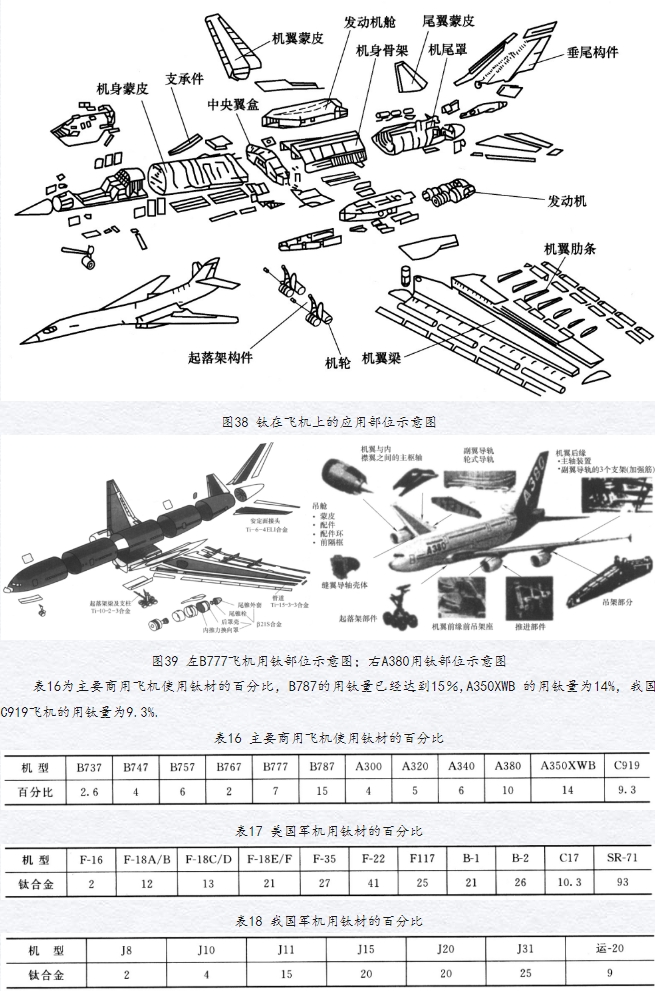
As a structural material for aircraft bodies, titanium alloy can be used as a fireproof wall, engine nacelle, skin, frame, longitudinal beam, hatch cover, keel, quick acting brake, fastener, landing gear beam (support beam), front wheel, arch frame, partition cover plate, flap slide rail, belly plate, etc. Figure 40 shows a schematic diagram of the titanium parts used in the aircraft body of Airbus A350XWB and domestic aircraft C919, including landing gear, wing structure, engine suspension, wing high-pressure oil and gas pipes, fasteners, cabin doors, cabin panels or partitions, seat rails, tail cones, and thermal insulation screens for the auxiliary power cabin.
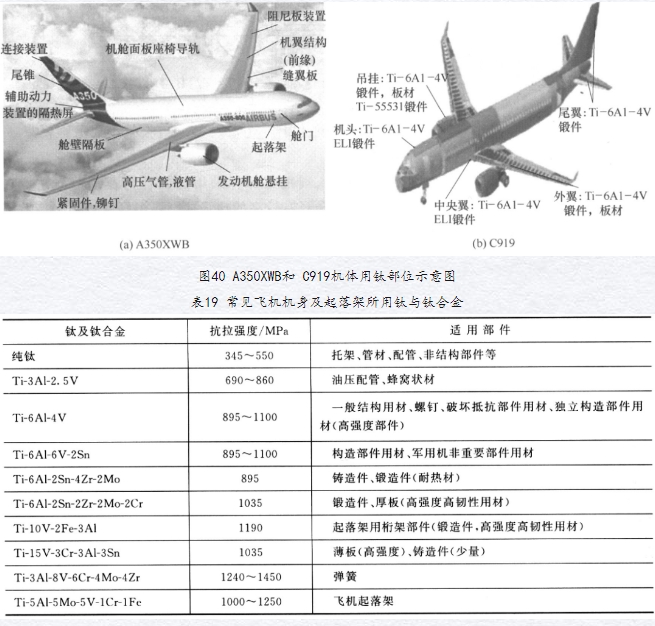
As the heart of an aircraft, the higher the thrust to weight ratio of the engine, the better, but the higher the material requirements. Figure 41 is a schematic diagram of the titanium parts used in jet engines, where the black area represents titanium alloy, mainly used for compressor fan discs, fan blades, medium/high pressure compressor discs, moving blades, stationary blades, ducts and other components. Due to its excellent high-temperature performance, titanium alloy has become the main choice for engine compressor blades and discs. The development of high-temperature titanium alloy has always been driven by the demand for advanced aviation engines.
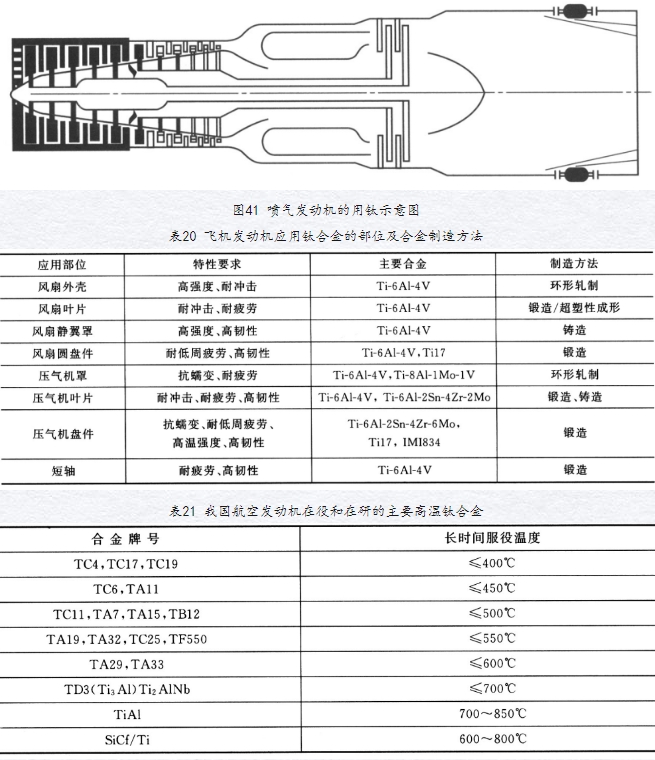
2. Aerospace titanium alloys
Industrial pure titanium and Ti-6AI-4V, Ti-5AI-2.5Sn, Ti-6AI-4V ELI, Ti-5AI-2.5SnELI, Ti-7A1-4Mo, Ti-3A1-2.5V, Ti-15V-3Cr-3Sn-3A1, Ti-13V-11Cr-3A1, Ti/B Al composite materials have been widely used in the aerospace field.
Titanium and titanium based alloys are used in structural components of aerospace vehicles such as missiles, launch vehicles, artificial satellites, and spacecraft, achieving the goal of reducing launch weight, increasing range, and saving launch costs. In rockets and missiles, titanium alloys are mainly used for fuel storage tanks, rocket engine casings and rings, rocket nozzle sleeves, etc. In artificial Earth satellites, titanium alloys are mainly used for shells, support frames, fuel storage tanks, and recovery module end frames. Titanium nickel shape memory alloys can be used for temperature control system components, and titanium castings can be used for resource satellite camera frames.