1、 The source of titanium metal
Titanium metal was first discovered by an amateur mineralogist named Gregor in England in 1791. By 1795, German chemist Klaplus named this unknown metallic substance after the Greek god Titans, which is translated as "titanium" in Chinese and English.
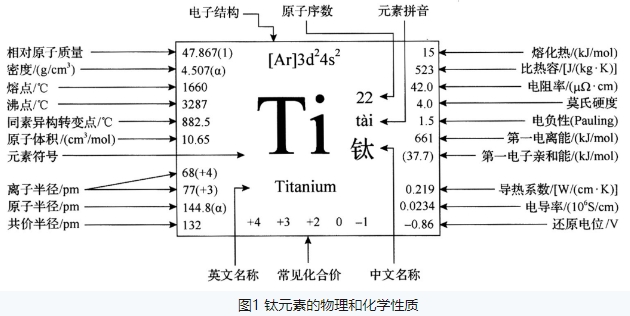
Titanium is recognized as a non-toxic element worldwide, with high extraction and production costs and high prices. Due to a series of qualifications such as high and low temperature resistance, strong acid and alkali resistance, high strength, and low density, it has become a specialized material for NASA's rocket satellites and has also been applied in China's super projects such as the Yutu, J-20, and Shandong carrier. After entering the civilian field in the 1980s, it became the "Honorary Metal King" in the food industry due to its natural antibacterial and biological properties.
China's titanium industry started in the 1950s, and by the mid-1960s, China had built sponge titanium and titanium processing production plants in Zunyi and Baoji, respectively. This means that China has become one of the world's top titanium industry powers. In the 21st century, China's titanium industry has entered a new era of accelerated development, with titanium production capacity ranking among the top in the world.
2、 The difference between pure titanium and titanium alloys
Pure titanium, also known as industrial pure titanium or commercial pure titanium, is classified according to the content of impurity elements. It has excellent stamping process performance and welding performance, is not sensitive to heat treatment and microstructure type, and has a certain strength under satisfactory plastic conditions. Its strength mainly depends on the content of interstitial elements oxygen and nitrogen.
Titanium alloy: Titanium alloy is an alloy composed of titanium as the basis and other elements, belonging to a relatively young metal with a history of only 60-70 years since its discovery.
Titanium alloy materials have the characteristics of light weight, high strength, low elasticity, high temperature resistance, and corrosion resistance, and are mainly used in components such as aviation engines, rockets, and missiles.
Titanium has two types of homogenous crystals; Titanium is a homoisomer with a melting point of 1720 ° C. It exhibits a dense hexagonal lattice structure below 882 ° C, known as α- Titanium; It exhibits a body centered cubic lattice structure above 882 ° C, known as β- Titanium, utilizing the different characteristics of the two structures mentioned above, adds appropriate alloying elements to gradually change its phase transition temperature and phase content, resulting in titanium alloys with different microstructures.
Titanium alloy elements can be classified into three categories based on their influence on phase transition temperature:
① Stable α The elements that increase the phase transition temperature are α Stable elements include aluminum, magnesium, oxygen, and nitrogen. Aluminum is the main alloying element of titanium alloy, which has a significant effect on improving the room temperature and high temperature strength of the alloy, reducing the specific gravity, and increasing the elastic modulus.
② Stable β The elements that lower the phase transition temperature are β Stable elements. It can also be divided into two types: isomorphic and eutectoid, with the former consisting of molybdenum, niobium, vanadium, etc; The latter includes chromium, manganese, copper, silicon, etc.
③ Neutral elements such as zirconium and tin have little effect on the phase transition temperature.
3、 The application of titanium and titanium alloys
Although titanium and titanium alloy materials have abundant reserves, their prices are very expensive. This is because titanium has low chemical activity under high temperature conditions, and its smelting technology and operating environment are very strict. It must be smelted under high temperature and vacuum conditions, often reaching temperatures above 800 ℃, which is much more difficult than steel and iron smelting. Therefore, whenever titanium alloy is mentioned, people feel that it is a high-end metal material with low production and high price, and few applications.
At present, due to the excellent properties of titanium alloy, such as light weight, high strength, and high temperature resistance, titanium and titanium alloy materials are widely used in the manufacturing of cutting-edge weapons and national heavy weapons in various countries, especially suitable for application in the aerospace field. Examples of application areas are as follows:
Chemical industry
Alkali industry: The emergence of titanium alloy refrigerators can effectively solve the problem of producing substandard chlorine gas due to the unreasonable traditional cooling process. At the same time, it has changed the production landscape of the chlor alkali industry, and the service life of titanium alloy refrigerators invested can reach up to 20 years.
Salt making industry: Currently, the most advanced salt making process is vacuum salt making, and the high-temperature concentrated salt water generated during this process can cause serious damage to the carbon steel structure, resulting in equipment leakage. The use of titanium steel composite structure in heating and evaporation chambers can effectively prevent salt scaling, improve salt production quality, and reduce the corrosion of high concentration salt water on the pipe wall during the evaporation process, thereby extending the maintenance period.
Aerospace field
Aviation industry: The application of titanium alloys is divided into aircraft structural titanium alloys and engine structural titanium alloys. The main application areas of titanium alloy structural components in aircraft include landing gear components, frames, beams, fuselage skins, heat shields, etc; In terms of aviation engines, titanium alloys are mainly used in compressor discs, blades, drums, high-pressure compressor rotors, compressor casings, etc.
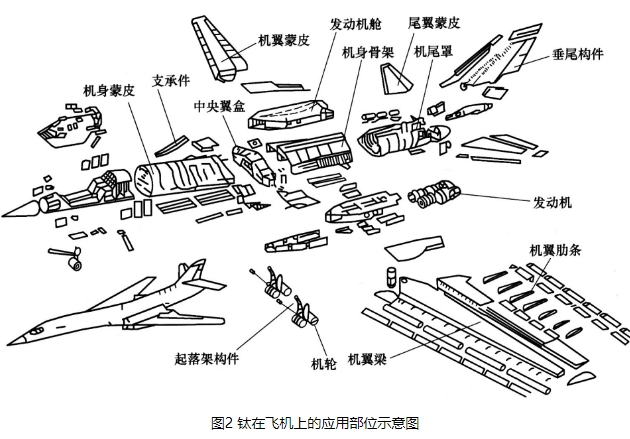
Aerospace industry: The working conditions of aerospace vehicles are extremely extreme. In addition to the need for advanced technology in material structural design, the excellent characteristics and functions of materials themselves are also important. Therefore, titanium alloys stand out among many materials. In terms of aerospace equipment, in the 1960s, the wing beams and ribs of the manned and enclosed compartments of the American Apollo program spacecraft were made of Ti-5Al-2.5Sn, while the lining was made of pure titanium; German MT Aerospace Company has prepared a high-strength Ti-15V-3Cr alloy propulsion system storage tank and applied it to the European Alpha communication satellite giant platform; There are many examples of the application of Russian titanium alloys in aerospace engineering, such as the use of BT23 titanium alloy large die forgings and forgings weighing 3.5 tons in the energy launch vehicle; In addition, titanium alloys are also used in fuel tanks, low-temperature liquid storage tanks, and impeller pumps for liquid fuel rocket engines.
Similarly, with the rapid development of domestic aerospace engineering, titanium alloys have also been widely used. From the Dongfang-1 satellite in 1970 to the current Shenzhou series spacecraft and Chang'e probe, titanium alloys have been used. In addition, low-temperature TA7ELI titanium alloy cylinders developed in China for use in liquid hydrogen environments have been used in the Long March series launch vehicles; Harbin Institute of Technology used TC4 titanium alloy to prepare the wheels of the lunar rover; In addition, China also uses high-strength titanium alloys such as BT20 to manufacture components such as missile engine casings and nozzles.
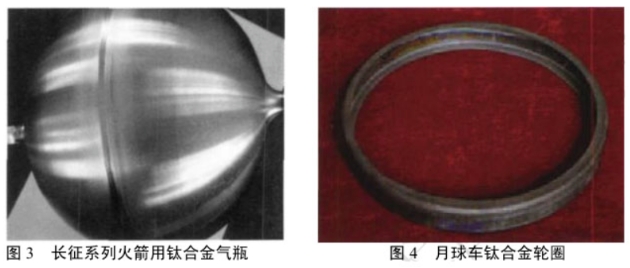
Ship field
Titanium and titanium alloys are widely used in nuclear submarines, deep submersibles, atomic energy icebreakers, hydrofoils, hovercraft, minesweepers, as well as propeller propellers, whip antennas, seawater pipelines, condensers, heat exchangers, acoustic devices, and firefighting equipment. The American deep-sea submersible "Haiya" is equipped with a titanium observation module and a control module; Japan's Toho Titanium Corporation and Fujishin Shipyard jointly built the "Molitshita II" all titanium speedboat; The Jiaolong, China's first independently designed and integrated manned submersible, also uses titanium alloy.
4、 Research on corrosion behavior under different service conditions
Titanium and titanium alloys may experience pitting corrosion, stress corrosion, and galvanic corrosion during service, making it extremely important to study the corrosion behavior of titanium and titanium alloys.
Ocean Engineering:
Titanium and titanium alloys are lightweight, high-strength, and corrosion-resistant, earning the reputation of being "ocean metals". In recent years, they have gradually replaced stainless steel in marine engineering for application. The marine environment is extremely harsh, and the surface seawater is a natural electrolyte with high salt content and strong conductivity. The chloride ions in seawater can also damage the passivation film on the surface of titanium metal. As the depth of deep submersibles diving into the ocean increases, materials will withstand enormous hydrostatic pressure. Hydrostatic pressure affects the corrosion resistance of materials by promoting pitting corrosion and damaging surface passivation films. At the same time, the salt content, oxygen content, pH value, and temperature in seawater will change with the depth of the ocean, causing different effects on the corrosion behavior of titanium materials.
Domestic and foreign researchers have conducted various studies on the corrosion behavior of titanium and titanium alloys in marine environments, and found that deep-sea environments can promote the corrosion of TA2 pure titanium and TC4 titanium alloys; Hydrostatic pressure can promote the uniform corrosion and cathodic hydrogen evolution reaction of TA2 pure titanium. When the hydrostatic pressure increases to a certain extent, the corrosion current density increases with the increase of hydrostatic pressure; There are trace sulfides in the deep-sea environment, which can cause a decrease in the stability of TA2 pure titanium passivation film; A higher hydrostatic pressure will increase the stress corrosion sensitivity of TC4 titanium alloy, reduce the content of TiO2 in the passivation film, and a higher oxygen solubility can reduce the stress corrosion sensitivity of TC4 titanium alloy; Ti80, Ti75, and Ti31 alloys do not exhibit significant stress corrosion tendencies in simulated deep-sea environments; The static water pressure has no significant effect on the stress corrosion sensitivity of Ti75 alloy, and the critical potential for hydrogen induced stress corrosion of this alloy is -0.77V.
Although significant achievements have been made in the corrosion behavior of titanium and titanium alloys in marine environments, there are still some gaps between simulation conditions and actual working conditions, which limits the practical guidance of these achievements for marine engineering. It is urgent for engineering personnel to improve the relevant deep-sea simulation experimental equipment. In addition, with the rapid development of China's deep-sea industry, there is an urgent need to develop new titanium alloys to meet the complex and ever-changing harsh environment of the deep sea, which will also be one of the important research directions in the field of titanium and titanium alloys in the future.
Aviation industry:
In the aviation industry, titanium alloys are widely used as mid end compressor blades, facing challenges in high temperature, high pressure, and complex airflow environments. With the upgrading of aircraft engine thrust, the working temperature of titanium alloy blades is also increasing. At high temperatures, the oxidation rate of titanium alloy is quite fast, causing severe corrosion of titanium alloy blades. At the same time, the generated oxides will also reduce the bearing area of the parts.
On the other hand, under marine service conditions, the engine of carrier based aircraft will also face tropical marine environments with high humidity and high salt spray, and a mixed salt film will form on the surface of titanium alloy blades.
In addition, during the transition between engine operation and parking, titanium alloy blades also undergo alternating dynamic corrosion between wet and dry states, seriously affecting their service life in high-temperature environments.
However, considering all factors, titanium alloy remains one of the most promising materials in aviation engines, and conducting systematic research on high-temperature corrosion failure theory of titanium alloy is of great significance.
In recent years, research has found that TA15 titanium alloy is very sensitive to hot salt stress corrosion during the corrosion process α Complex chemical reactions occur at the phase boundary, resulting in the diffusion of corrosive oxides into the matrix, severely reducing the material's durability; At 600-700 ℃, the initial oxidation reaction of Ti650 alloy is more intense, and after more than 50 hours of oxidation, it tends to stabilize. The oxidation reaction index n is greater than 2, and the main product of the oxidation reaction is granular TiO2; For TA2 pure titanium and TC4 and Ti60 alloys, Ti60 alloy has the strongest high-temperature oxidation resistance, and its oxidation process is controlled by diffusion. However, at 800 ℃, the precipitation of Sn and Nd rich phases induces the peeling of the oxide film, resulting in a decrease in the oxidation resistance of Ti60 alloy.
The first issue that titanium alloys face in the aviation industry is high-temperature oxidation, and researchers have conducted extensive research on this issue. However, in recent years, China has vigorously built the Deep Blue Navy, and the service environment of its carrier based aircraft is significantly different from that of inland areas. In deep-sea environments such as the South China Sea, titanium alloy components on carrier based aircraft engines will face harsh corrosion conditions such as high temperature, high humidity, and high concentration of salt spray. Currently, there is relatively little research on this aspect, and it will be one of the important development directions of titanium alloys in the future.
Oil and gas extraction and chemical industry:
Titanium and titanium alloys are gradually being applied in acidic conditions such as oil and gas extraction and chemical industry due to their excellent corrosion resistance. Therefore, domestic and foreign researchers have conducted extensive research on the corrosion behavior of titanium and titanium alloys under acidic conditions.
Research has found that Ti-6Al-4V, Ti-6Al-4V-0.1Ru, Ti-6Al-2Sn-4Zr-6Mo, Ti-3Al-8V-6Cr-4Zr-4Mo, and Ti-5.5Al-4.5V-2Zr-1Mo, commonly used titanium alloy materials for oil and gas development, exhibit anodic control in their corrosion reactions under the tested operating conditions, with uniform corrosion rates below 0.001 mm/a and good resistance to stress corrosion cracking; In actual working conditions, as the pH value decreases, the self corrosion potential of all titanium alloys will decrease, the polarization resistance will decrease, the corrosion current will increase, and the corrosion resistance will decrease; The immersion test and electrochemical characterization of Gr.2 pure titanium and Gr.7 titanium alloy were conducted in five different strong reducing acids. The study found that the corrosion of Gr.2 pure titanium and Gr.7 titanium alloy was most severe in sulfuric acid, and within a certain testing time, the higher the temperature of the corrosion medium, the higher the corrosion rate.
Titanium metal has great potential application value in fields such as oil and gas extraction and chemical industry. In this direction, researchers still focus on how to improve the corrosion resistance of titanium and titanium alloys in acidic environments (reducing acids such as hydrochloric acid and hydrofluoric acid) and enhance their applicability in acidic environments.
5、 Surface treatment technology for titanium and titanium alloys
In recent years, in order to further improve the corrosion resistance of titanium and titanium alloys to meet more stringent service environments, researchers have conducted extensive research on their surface treatment technologies. At present, the commonly used surface treatment technologies for titanium and titanium alloys include micro arc oxidation, vapor deposition (physical/chemical), ion implantation technology, surface coating technology, etc.
Research has shown that the micro arc oxidation film layer prepared on the surface of TC4 titanium alloy using the micro arc oxidation+high-temperature oxidation+silane sealing treatment process can effectively protect TC4 titanium alloy; Graphene nanocoating has a long-term protective ability against TC4 titanium alloy. Even after long-term immersion in strong acidic corrosive media (pH 2.0), the nanocoating still exhibits very high structural integrity, with a coating coverage area greater than 98%; A uniform and dense Al/Cr composite coating without defects such as pores and cracks can be prepared on the surface of Ti2AlNb alloy using dual glow plasma surface chrome infiltration and magnetron sputtering aluminum plating process. The thickness of the coating is about 73 μ m. From the surface to the inside, it can be clearly divided into four layers: Al deposition layer, Al/Cr alloy layer, Cr deposition layer, and Cr diffusion layer, which can significantly improve the hot corrosion resistance of Ti2AlNb alloy matrix in Na2SO4 molten salt environment.
6、 Existing problems and corrosion research directions of titanium and titanium alloys
Although titanium and titanium alloys have made significant progress, existing problems have also been exposed, posing significant challenges for the development of titanium alloys. Mainly reflected in the following three aspects:
(1) In terms of output. Although China is a major titanium industry country, the quantity of high-quality products in production is not high, and there are few types of special performance titanium products. Secondly, China is unable to produce titanium strips and extruded titanium profiles in bulk and stably, which limits the development and utilization of titanium and titanium alloys in aerospace, marine and other fields. It is still very difficult to further increase the amount of titanium used in aviation engines to around 50%.
(2) In terms of performance. Due to the high chemical activity of titanium metal and its susceptibility to contamination by other elements, the processing and manufacturing processes of titanium alloys are very high. At the same time, the high-performance products processed need to comprehensively consider their mechanical, physical, chemical, and process properties. Existing titanium alloys have a temperature above 600 ℃, and the sharp decline in creep resistance and high-temperature oxidation resistance is the two main obstacles that limit the expansion of titanium alloy applications.
(3) In terms of cost. At present, various countries are striving to reduce the application cost of titanium alloys and have achieved many achievements. However, in terms of the current situation in China, the management and technical level have not yet reached the ideal level, and domestic titanium alloy products have poor competitiveness in the international market, which is not conducive to further expanding their use.
With the successful use of titanium and titanium alloys in marine engineering, aviation industry, oil and gas development, chemical industry, and other fields, fundamental research on their corrosion behavior has been greatly promoted. However, with the rapid development of technology and industry, the service environment of titanium and titanium alloys is becoming increasingly harsh and complex. Given the current market demand and challenges faced by titanium and titanium alloys, the future research directions for corrosion behavior of titanium and titanium alloys mainly include the following aspects:
1. On the basis of existing research, we will delve into the corrosion failure behavior and protection techniques of titanium and titanium alloys under the coupling effect of multiple influencing factors (corrosion medium, temperature, stress).
2. Emphasis is placed on using numerical simulation and other methods to explore the corrosion mechanism of titanium and titanium alloys at the micro scale, and optimizing the alloy composition. Gradually, a database of corrosion performance and processing parameters of titanium and titanium alloys is established, providing data and theoretical support for the development of new corrosion-resistant titanium alloys, reducing research and development costs, and improving research and development efficiency.
3. Further reduce the cost of various surface treatment technologies, and combine existing surface treatment technologies of titanium and titanium alloys to comprehensively develop "multi technology composite protection" technology, and conduct in-depth research on corrosion and protection mechanisms. In the future, researchers will delve deeper into new surface treatment technologies that are more suitable for improving the comprehensive properties of titanium and titanium alloys.