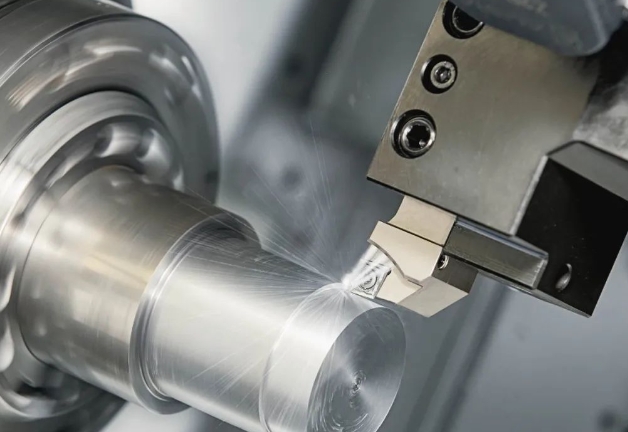
Titanium alloy has many advantages. For example: high corrosion resistance, low density and high strength, non-magnetic, biocompatibility, high temperature resistance, etc. However, titanium alloys are actually difficult to process and require special cutting tools. This article will discuss why titanium alloys are difficult to process and what countermeasures are available.
1. The reasons why titanium alloys are difficult to process
Firstly, temperature concentration
The thermal conductivity of most titanium alloys is very low, only 1/7 of steel, 1/16 of aluminum, and 1/25 of copper. Therefore, the heat generated during the cutting of titanium alloy will not be quickly transferred to the workpiece or carried away by the chips, but will be concentrated in the cutting area.
The temperature generated by the cutting edge can reach up to 1000 ℃, causing rapid wear and cracking of the cutting edge of the tool, resulting in chip accumulation and shortening the tool life.
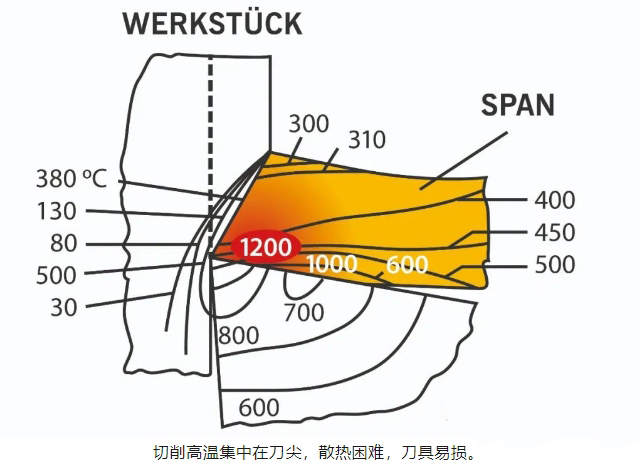
The high temperature generated during the cutting process also damages the surface integrity of titanium alloy parts, leading to a decrease in geometric accuracy of the parts and the occurrence of work hardening, seriously reducing their fatigue strength.
Secondly, elastic deformation
The elastic modulus of titanium alloy is not very high, for example, the elastic modulus of TC4 is only 110Gpa, while the elastic modulus of 45 steel is 210Gpa, and the elastic modulus of stainless steel such as 303304316 is also around 200Gpa. Therefore, when processing titanium alloy, elastic deformation is prone to occur.
When processing thin-walled or circular parts, this problem is more serious. It is not easy to process titanium alloy thin-walled parts to the expected dimensional accuracy. Because when the workpiece material is pushed away by the tool, the local deformation of the thin-walled part has exceeded the elastic range, resulting in plastic deformation, and the strength and hardness of the cutting point material significantly increase.
The cutting pressure causes the "elastic" workpiece to leave the tool and rebound, resulting in greater friction between the tool and the workpiece than the cutting effect. The friction process generates heat, exacerbating the problem of poor thermal conductivity of titanium alloys.
Thirdly, titanium alloy has a good affinity, which leads to the formation of long and continuous chips during turning and drilling processes, which can entangle the tool and hinder its function. When the cutting depth is too deep, it can cause tool sticking, burning, and fracture.
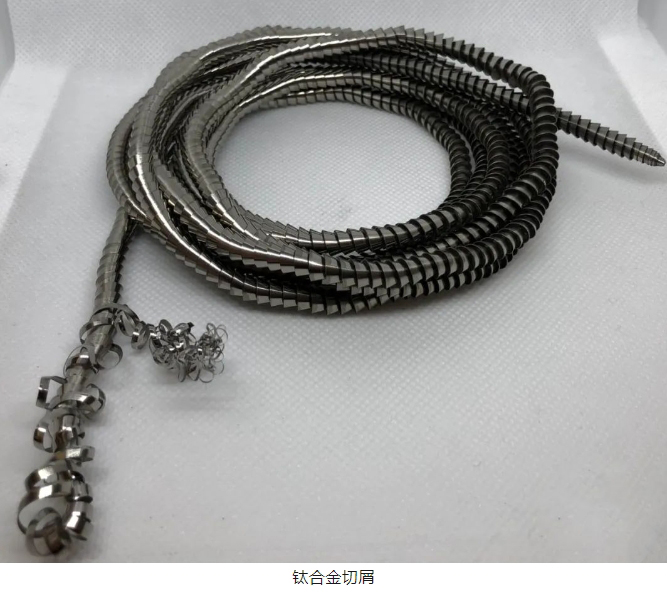
Of course, affinity is also quite useful in other places, such as in ion pumps, which are used to make titanium cathode plates. When titanium atoms are splashed onto the anode tube wall, they can adsorb gas and generate ultra-high vacuum.
Fourthly, vibration
The elasticity of titanium alloys may be beneficial for the performance of parts, but during the cutting process, the elastic deformation of the workpiece is an important cause of vibration.
The vibration generated by processing titanium alloy is approximately 10 times that of steel. Due to the concentration of cutting heat on the cutting part, sawtooth shaped chips are generated, leading to fluctuations in cutting power.
2. Countermeasures for Difficult Processing of Titanium Alloy
Firstly, cooling
Coolants can be used to reduce the high temperature generated during the cutting process. Typically, non soluble oil coolants are used for low-speed heavy-duty cutting and shearing, while soluble cutting coolants are used for high-speed cutting or shearing.
In addition, low-temperature cutting method can be used, using liquid nitrogen (-180 ℃) or liquid CO2 (-76 ℃) as cutting fluid to reduce the temperature of the cutting zone. This method can reduce the main cutting force by 20%, lower the cutting temperature by more than 300 ℃, eliminate chip deposits, improve the machining surface quality, and increase tool durability by 2 to 3 times.
Secondly, choose the appropriate tool
Choosing the right cutting tool can lead to significant improvements.
Due to the fact that heat must be discharged through the cutting edge and coolant, rather than through the chips like steel, a small portion of the cutting edge must withstand extremely high thermal and mechanical stresses, using sharp cutting edges to reduce cutting force.
In addition, cutting pressure can be reduced by using grinding with polished grooves and high angle indexable blades.
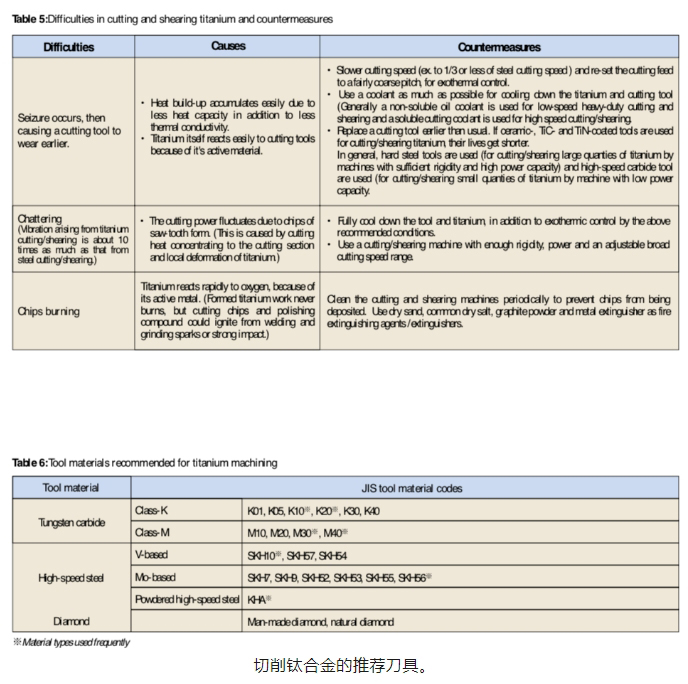
If necessary, coated cutting tools can also be used to resist the viscosity of the alloy and break long chips, thereby minimizing friction during chip removal, which helps prevent heat generation during the machining process.
Thirdly, constant feed or increasing feed rate
Titanium is prone to work hardening, meaning that when cutting materials, titanium becomes harder and therefore more prone to tool wear. Constant feed ensures that work hardening is kept to a minimum.
Of course, if the machine allows, the feed rate can be increased, which means that the tool spends less time in a specific area, so there is no more time for heat accumulation and work hardening.
Fourth, reduce cutting speed
For example, using a steel cutting speed of 1/3 or lower for heat release control.
Fifth, replace the cutting tools according to the process
Ceramic, titanium carbide, and titanium nitride coated cutting tools are used for processing titanium alloys and have a shorter lifespan. Typically, hard rigid cutting tools are used to cut large amounts of titanium, while high-speed hard alloy cutting tools are used to cut small amounts of titanium.
Currently, ultrasonic machining is being developed with the goal of reducing tool contact time and extending tool life.
Sixth, use high rigidity machine tools
A sturdy and durable machine tool is crucial for successfully processing titanium alloys.
The ideal titanium alloy milling machine must be rigid, and the spindle must be able to operate at low speeds and high torques.
This helps to absorb vibrations and reduce chatter during the cutting process, which is a common problem when machining titanium alloys.
Finally, processing equipment and tools should be regularly cleaned to prevent debris deposition.