Foil is a thin metal sheet, such as tin foil, copper foil, aluminum foil, etc. Specifically, all metal sheets with a thickness of less than 0.2mm are called foil. According to the thickness of metal foil, it can be divided into thick foil, single zero foil and double zero foil. The thickness of thick foil is < 0.2mm - ≥ 0.1mm, the thickness of single zero foil is < 0.1mm - ≥ 0.09mm, and the thickness of double zero foil is ≤ 0.001 mm. The thickness of the thinnest foil that can be rolled industrially is 0.0045mm. At present, the output of aluminum foil is the largest, accounting for almost 85% of the total output of metal foil in the world. China is the world's largest producer and exporter of aluminum foil. In 2020, the output will reach 4050kt, accounting for about 65% of the global total, and the export volume will account for 30% of the output, reaching 1215kt.
Titanium foil is difficult to produce, expensive, and low in output. It is estimated that the world's output will not exceed 20 tons in 2020. The main country of production is the United States, and its use is not wide. Aircraft skin insulation materials are one of its high-end applications. As we all know, when an aircraft flies in the air, its outer metal skin will heat up due to fierce friction with the air and other reasons. In order to prevent heat from flowing into the interior, it is necessary to set up a thermal insulation protective layer (Figure 1). It is welded by four layers of heat shields, with a thinner flat plate sandwiched in the middle. Figure 2 is the part drawing of heat insulation panel, which is made of 0.08mm TB2 alloy foil. TB2 is a kind of β Type I titanium alloy, Ti-5Mo-5V-8Cr-3Al alloy (mass%): Al2.5-3.5, Mo4.7-5.7, V4.7-5.7, Cr7.5-8.5, Fe0.30, C0.05, N0.04, H0.015, O0.15, other impurities 0.1, 0.4 in total, the rest Ti.
The United States, France and other countries use the superplastic forming process to process this titanium foil insulation plate. However, although this process can process high-quality insulation plates, the production cycle is long, and the workpiece is in a high temperature state for a long time, it will more or less absorb oxygen. Titanium no longer has the ability to resist oxidation above 649 ℃, it will absorb more oxygen and become brittle, making its mechanical properties decline comprehensively. In addition, superplastic forming is suitable for preparing workpieces with simple shapes. For complex workpieces shown in Figure 2, it is difficult to superplastic forming, because it is not easy to process molds.
As the heat insulation plate is diffusion welded, the oxygen content should be precisely and strictly controlled, so it is better to weld in the vacuum furnace, but this requires expensive equipment, increases investment, and increases the difficulty of operation. To this end, Cheng Xiuquan of Beijing Institute of Aeronautical Technology and others proposed to successfully prepare qualified low-cost, high-quality and efficient titanium foil aircraft thermal insulation panels by using a semi coupling mold and a jacket protection process. The results were good and highly praised by users.
During production, TB2 alloy foil shall be placed in the sheath first, and the oxygen in the sheath shall be removed before hot forming, which can be removed by conventional vacuum method, and the sheath shall be sealed after suction. Attention shall be paid to the following matters when using the sheath technology: carefully clean the oil stain and sundries on the titanium sheet and the surface of the sheath, and be sure to be clean; The jacket materials shall be strictly selected, which shall not leak under high temperature and shall not emit any gas. Materials with low high temperature strength shall also be selected as far as possible to reduce deformation resistance, improve mold life and ensure the dimensional accuracy requirements of the workpiece; A thin and uniform layer of solder stop shall be coated on the jacket to avoid welding between the jacket and titanium foil. However, the solder stop shall not emit any harmful gas under high temperature and shall not contain water, glue and other substances.
The prepared jacket shall be formed at 750 ℃, and the pressure shall not be too high. The jacket shall be preheated for 1 min to 2 min, and maintained for 20 s to 30 s. The jacket shall be taken out, and the workpiece can be taken out after it is cooled. The surface brightness of the workpiece is almost the same as that of the original foil. The measured results show that the oxygen content in the surface layer is less than 200ppm, and the thickness of the oxide layer does not change. It can be seen that the sheath not only protects the workpiece from pollution, but also bears most of the uneven deformation, greatly improving the deformation uniformity of the workpiece. The measured thickness of the deformed workpiece is 0.067mm-0.072mm, which is completely within the deviation range of the original foil thickness.
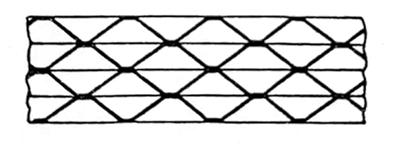
Fig. 1 Sectional View of Insulation Layer
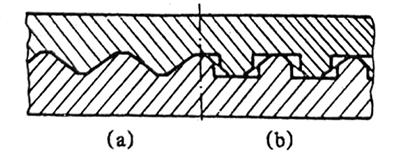
Fig. 2 Parts of heat shield
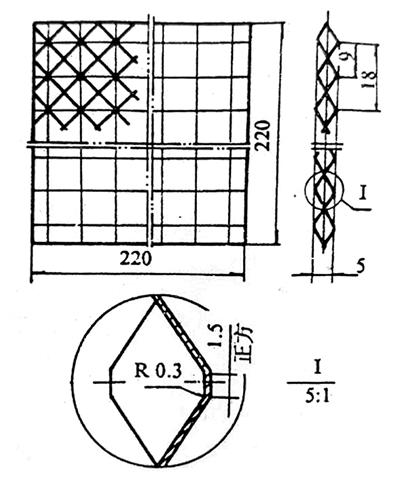
Fig. 3 Two die structures