增材制造(AM)是一项革命性的技术,为材料加工和设计提供了不同的途径。AM在很大程度上被认为是一种直接成型材料零件的技术,而没有充分利用增材制造提供的合金和工艺协同进步的能力。通常而言金属材料中的成分不均匀性往往被看做材料内部的重大缺陷,是研究人员一直所努力避免的。然而,材料的成分不均匀性却很少被积极地利用起来作为有效的合金设计方法。一方面,这是由于人们对成分不均匀性的积极作用缺乏足够的认识;另一方面,也是因为传统的铸造、锻造等方法往往无法对材料内部的成分波动实现人为有效的调控。而AM在这精准调控成分波动方面却具有独特的优势。通过逐点、逐层地灵活构建组分,AM提供了创建具有特定位置成分和显微结构的异质合金的机会。
激光粉末床融合技术(L-PBF)是一种用于制造金属部件的增材制造技术之一,设计灵活且资源有效利用率高。近日,西安交通大学前沿科学技术研究院与香港城市大学联合培养的张天隆博士等人将成分调制的概念和3D打印技术结合起来。通过激光粉末床融合技术,采用两种常见合金粉末(Ti64和316L不锈钢)进行混合打印。通过精心选择的粉末种类,以及特殊的打印参数,在Ti-6Al-4V基础合金中,成功实现了以Fe元素为主的微米级成分梯度,构造出一个β+α’的双相微观结构,表现出渐进相变诱导塑性效应,具备优异力学性能的钛合金。
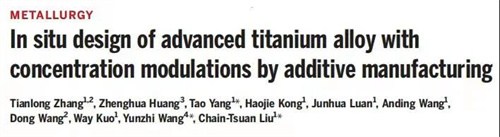
研究要点
Ti64合金存在粗大的柱状晶和加工硬化能力差的问题。316L中的元素(Fe、Cr、Ni、Mo)是有效的晶粒细化剂,也是钛合金β相的有效稳定元素。使用Ti-6Al-4V(Ti64)和316L(67.5Fe-18Cr-12Ni-2.5Mo,均为wt%)的混合物,通过L-PBF技术设计出这样微米级成分梯度的钛合金。通过选择合适的316L加入量和L-PBF工艺参数,所有合金元素都进行了有效的扩散和融合。不锈钢中的Fe、Cr、Ni、Mo等元素完全溶解在Ti64合金基体中,实现了原位合金化,形成了精细调制的β+α′双相组织。这种微米级成分梯度钛合金在变形过程中在较宽的外部载荷范围下内表现出较高的屈服强度和渐进相变诱发塑性(TRIP)效应,极大地改善了增材制造钛合金的均匀变形和加工硬化能力。
1、微米级成分梯度带来的第一个有利影响是对所得合金的稳定性和微观结构的调节,形成了熔岩样的独特微结构。在每个单独的熔池区域内,有两种截然不同的微结构特征。利用EBSD证实了高度非均匀和精细调制的β+α′微观结构。
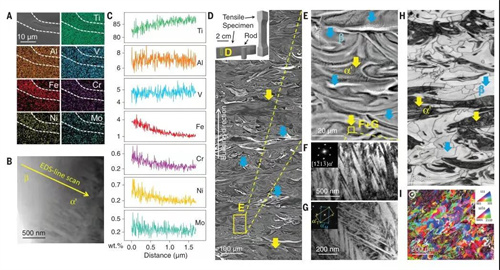
图1 微米尺度成分梯度结构和由此产生的熔岩状微观结构。
2、微米级成分梯度的第二个影响是对亚稳诱导的力学性能的提高。形成高度弥散的马氏体-亚稳态母相的双相组织使得合金具有优异的加工硬化能力。两相区域内的成分变化导致相稳定性变化,这导致加载时的渐进TRIP效应,使合金具有更长的均匀伸长率。此外超细化马氏体还为合金提供了高屈服强度。

图2 Ti64-x316L的微观组织和力学性能。
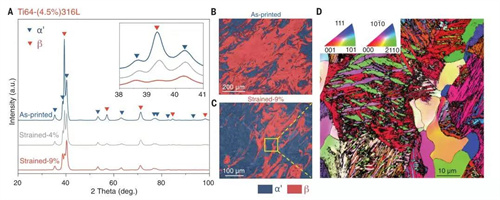
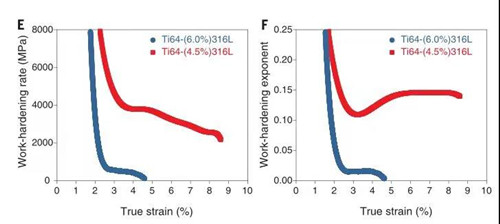
图3 微米级成分梯度合金的加工硬化行为和组织演变。
3、微米级成分梯度的第三个重要影响是晶粒细化。Fe、Cr等元素的添加有效提升钛合金凝固过程中的成分过冷能力,阻止了常规粗大柱状晶的形成。打印态的TI64-(4.5%)316L合金的晶粒尺寸只有约16微米,是目前所有增材制造钛合金中所能实现的最小晶粒尺寸之一。
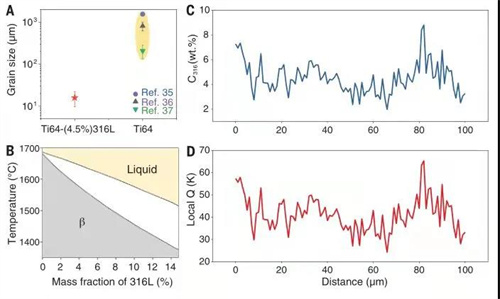
图4 微米级成分梯度对晶粒细化的影响。
研究内容展示了一种微米级成分梯度合金设计的方法,该方法通过精细尺度成分调制的L-PBF技术来实现具有优异机械性能的微结构。部分均匀化制备的微米级成分梯度 Ti64(4.5%)316L合金具有细小且高度分散的马氏体α’+亚稳态β双相组织混合物,晶粒细小(16 μm),超细化相区提供了高屈服强度,在较宽的应力范围内具有渐进的TRIP效应,具有1.3 GPa的高抗拉强度、9%的均匀延伸率和>300 MPa的优异加工硬化能力。